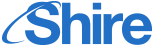
Job Information
Dairyland Power Cooperative Reliability Engineer I or II (On-Site - Alma, WI) in Alma, Wisconsin
Are you ready to join an organization where we focus on People First, have fun at work and make a difference in what we do?
Dairyland is proud of our People First culture centered around appreciation, celebrating wins and collaboration. We’ve worked hard to ensure alignment between our culture and our processes and systems, learning and development and rewards and recognition programs.
As a team, we work together to leverage the team’s diverse perspectives, ideas and experiences to deliver nothing less than the best. We are collaborative, transparent and committed to our People and their work experience, growth and professional development.
Hiring Salary Range:
Reliability Engineer I - $65,300 - $98,000
Reliability Engineer II - $84,500-$126,800
Compensation is determined by a combination of factors, including but not limited to education, work experience, and certifications. The actual offer may vary, reflecting the candidate's unique blend of experience, educational background, and skill level.
The Impact You'll Have in this Role:
This position will provide expert level on-site reliability and maintenance engineering functions and continuous improvement process for the station(s). To identify, research, evaluate, test and assist site level personnel to improve operating and maintenance practices leading to efficiencies for the stations by correcting problems and leading initiatives. To assist in the analysis and documentation of maintenance and capital improvements on site. To direct JPM’s predictive maintenance programs including Vibration Analysis, Oil Analysis, Thermography, and Ultra Sound programs.
Actively support, promote, and lead safety initiatives. Follow all safety policies and procedures. Always work safe and report any unsafe work or work environments to management.
Pursue all phases of new installations or major replacements on site. Assist in identification and development of project costs and schedules as required, especially in relation to long range projects. Develop and evaluate bid specifications to include replacement, upgrades and labor contracts for major equipment or systems.
Development and systemization of new PMs/PdMs required by new equipment. Support and promote station’s overall work management philosophy for existing equipment.
Assist in implementing training and maintenance procedures to ensure that station reliability and availability are unaffected by the work and that the plant remains in full compliance with regulatory guidelines, licenses and within technical specifications.
Assist in the development of improved operational and maintenance processes. Develop long term planning for maintenance of large rotating equipment (includes performance analysis, preventative maintenance, and repair/rebuild activities).
Assist in researching and developing opportunities to achieve lower cost station operations, as well as planned corrective or supportive actions through improved maintenance policies and technologies.
Assist the plant management team in evaluating and instituting procedures and initiatives that provide for the efficient operation and maintenance of the station(s).
Support the utilization of the CMMS for planning and scheduling work at the station(s). Identify opportunities to maximize the use and effectiveness of the CMMS system to facilitate better maintenance processes at the site.
Identify opportunities to reduce overall inventory.
Act as the primary performer for the reliability function at the station(s), i.e., evaluate break-ins, schedule compliance codes, PMs vs. reactive maintenance, root cause analysis, incident reporting root cause, OEM advisory and administrative control procedures.
Coordinate and implement major projects, perform Project Manager duties to represent the interest of DPC when major projects are implemented. Ensure contractor performance and services are in compliance with the work identified in the bid proposal. Ability to work with multiple contractors and project simultaneously.
Maintain a high degree of initiative to research solutions and process improvements to plant equipment/processes without direct supervision or direction. Offer to seek solutions in support of the Maintenance Manager and plant staff. Provide unbiased information and suggestions for improvement and solutions to problems. Provide the necessary financial information relating to solutions and improvements as required by the DPC budget process.
Conduct monthly plant reliability meetings, discussing vibration reports, oil analysis reports, thermography and ultrasound reports, and provide recommended repair strategies to ensure optimal plant operational reliability.
MINIMUM QUALIFICATIONS:
Education & Experience
Level I - Bachelor’s degree in mechanical/electric engineering with two (2) years relevant experience.
Level II - Bachelor’s Degree in mechanical, electrical or other relevant engineering field, with a minimum of four (4) years relative experience.
Skills :
Knowledge of the operation, maintenance, design and construction of power generating facilities and related equipment.
Good verbal, written and interpersonal communication skills, with the ability to interface effectively with individuals at various levels both internally and externally.
Management training and administration skills. Awareness of pertinent regulations, codes, and standards.
Proficient computer skills.
Ability to work as a team player as well as independently.
Ability to navigate AMS Machinery Manager, analyze vibration spectrums and waveforms, assist in single plane and dual plane balancing, and perform phase readings and analysis.
Licenses and Certifications: Certified Level II, III, or IV vibration analyst.
Certified Machinery Lubrication Analyst I or II (MLA1/MLA2). Certified Reliability Leader (CRL) or equivalent.
Physical Demands: The physical demands described here are representative of those that must be met by an employee to successfully perform the essential functions of this job. While performing the duties of this job, the employee is regularly required to talk or hear. The employee frequently is required to stand/sit; walk; use hands/fingers to handle or feel; and reach with hands and arms. Must be able to climb (stairs, sky climber, confined spaces). Ability to wear breathing equipment (35 lbs.) and safety harness. Reasonable accommodations may be made to enable individuals with disabilities to perform the essential functions.
We are committed to providing our greatest asset, our People, with as many perks and benefits as possible. Some benefits of working with us include:
Health & disability benefits (medical, dental, vision, short & long-term disability)
Life insurance
Generous 401(k) and Pension Plans
Paid Time Off
Robust Wellness Program
New Flexible Work Program
Tuition Reimbursement
So much more!
Dairyland Power Cooperative is an equal opportunity employer. All applicants will be considered for employment without attention to race, age, color, religion, sex, sexual orientation, gender identity, national origin, veteran or disability status.
If you are an individual with disabilities who needs accommodation or you are having difficulty using our website to apply for employment, contact our HR Department at 608-788-4000.
With headquarters in La Crosse, Wis., Dairyland is a generation and transmission cooperative that provides wholesale energy for 24 electric distribution cooperatives and 17 municipal utilities in Wisconsin, Minnesota, Iowa and Illinois.
At Dairyland, we know that happy employees are the backbone of any good organization. By offering an excellent compensation and benefits package, opportunities for career growth and a supportive environment, Dairyland helps ensure a quality business and premier workplace.
Dairyland Power Cooperative is an equal opportunity employer. All applicants will be considered for employment without attention to race, color, religion, sex, sexual orientation, gender identity, national origin, veteran or disability status.