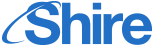
Job Information
Coca-Cola Bottling Company High Country Quality Control Manager in Bismarck, North Dakota
Quality Control Manager
Bismarck, ND (http://maps.google.com/maps?q=3225+E.+Thayer+Ave+Bismarck+ND+USA+58501)
Job Type
Full-time
Description
Coca-Cola, with its many brands, has been recognized and enjoyed by people around the world for over a century. Founded in 1956, Coca-Cola Bottling Company High Country is a family owned, regional Bottler serving portions of Colorado, Minnesota, Montana, North Dakota, South Dakota, Utah, and Wyoming.
Every day we honor our core values of Honesty, Integrity, Trust, and Respect through encouraging our team members to develop, grow and serve. Together we become more effective and productive… in life and work.
Refresh your career and join us in refreshing the world!
Apply Today!
Salary for the Quality Control Manager role is approximately $80,000 a year depending on experience.
Robust benefits package including 100% paid employee health, dental and vision!
100% Employer Paid Life Insurance for Employees
401K With Employee Match
Product Discounts
Much more!
What will you do as a Quality Control Manager?
As part of the Operations Team, the Quality Control Manager plans, coordinates, and directs quality control programs to ensure continuous production of products consistent with established standards.
ESSENTIAL DUTIES AND RESPONSIBILITIES
Develop and analyze statistical data and product specifications to determine present standards and establish proposed quality and reliability expectancy of finished product.
Formulate and maintain quality control objectives complementary to corporate policies and goals.
Create and implement inspection criteria and procedures.
Coordinate objectives with production procedures in cooperation with other plant managers to maximize product reliability and minimize costs.
Provide inspection activity for product throughout production cycle.
Apply total quality management tools and approaches to analytical and reporting processes within each department.
Direct workers engaged in inspection and testing activities to ensure continuous control over materials, facilities, and products.
Work with vendors to ensure quality of all purchased parts for company use.
Create and direct environmental test functions.
Assume active role on quality management teams within the organization.
Design and implement quality assurance training programs to key personnel in conjunction with managers.
Investigate quality index non-conformances and report findings to the Director of Manufacturing.
Knowledge of Management Systems and the ability to manage programs within the Management System.
Manage HAACP/HARPC programs and must have knowledge of the rules and regulations regarding Food Safety.
Keep up to date on information and technology affecting functional area(s) to increase innovation and ensure compliance and cost efficiencies.
Work with the leadership team to continuously foster a positive work environment, develop employee incentive programs, and establish the organization as a premier employer.
Work with the leadership team to develop strategic direction of the company including reviewing growth and expansion opportunities.
Conform with, abide by, and re-enforce all regulations, policies, work procedures, and processes.
JOB KNOWLEDGE, SKILLS AND ABILITIES
Problem solving and analytical skills.
Good computer skills in Word, Excel, and statistical based software
Ability to address and recognize business related issues.
Good written and oral communication skills.
Adaptability – Ability to adapt to change in the workplace.
Communication – Ability to effectively, clearly and concisely communicate verbally to both co-workers and customers.
Decision Making – Display willingness to make critical decisions while following company practices.
Delegation – Ability to delegate work, give authority to work independently, set expectations and monitor delegated activities.
Enthusiasm – Ability to bring energy to the day to day as well as long-term tasks and plans.
Judgment – Display willingness to make timely decisions and exhibit sound and accurate judgment.
Leadership – Ability to inspire and motivate others to perform well; accept feedback.
Planning & Organizing – Ability to prioritize and plan work activities, use time efficiently and develop realistic action plans.
Reliability – Demonstrate regular attendance and availability to staff and management.
Quality Management – Demonstrate commitment to improve and promote quality in all operating areas.
Safety & Security – Promote and personally observe safety and security procedures and use equipment and materials properly.
Honesty, Integrity, Trust & Respect – Must be seen as truthful and credible and exhibit respectful behavior in all actions representing the company.
SUPERVISORY RESPONSIBILITIES
Plan, direct, supervise and coordinate work activities of maintenance and production staff.
Coach and mentor staff in developing and achieving goals and objectives.
Provide regular performance feedback.
Instruct line leads in facilitating process improvement.
Requirements
EDUCATION AND EXPERIENCE
College Degree (with major emphasis in Chemistry, Biology, or Food Science) and a minimum of 2 years’ experience working in a quality control environment.
2-3 years relevant experience.
TRAINING REQUIREMENTS
Continuing education to maintain certification and a current working knowledge of applicable laws and regulations.
New Hire Orientation
Company’s Inter-Active Safety Training
Allergen Awareness Training
Diversity & Harassment Training
Reasonable Suspicion Training for Supervisors & Managers
Incident Management and Crisis Resolution Training
Consumer and Product Complaint Investigation and Response Training
PHYSICAL DEMANDS
Work involves walking, talking and hearing, using hands to handle, feel or operate objects. Vision abilities required by this job include close vision and the ability to focus when using computer terminals.
Must be able to lift 50 lbs. repetitively.
Must be able to stand for long periods of time.
PERSONAL PROTECTIVE EQUIPMENT (PPE)
Hearing protection dependant on specified areas.
Hard hat while on forklift
WORK ENVIRONMENT
The noise level in the work environment can be moderately noisy due to manufacturing and/or warehousing equipment in operation.
Some areas are slippery due to the production process.
Warehouse area has heavy forklift traffic.
This job description lists the major duties and requirements of the job and is not all-inclusive. Incumbent(s) may be expected to perform job-related duties other than those contained in this document and may be required to have specific job-related knowledge and skills.
Coca-Cola Bottling Company High country is an Equal Opportunity/Affirmative Action Employer, requires pre-employment drug testing for all applicable positions and adheres to an Alcohol and Drug-Free Workplace.
Salary Description
$80,000.00