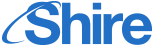
Job Information
L3Harris Senior Specialist, Welding Process Quality Engineering in Canoga Park, California
Job Title: Senior Specialist, Welding Process Quality Engineering
Job Code: QEP4
Job Location: Canoga Park, CA
Job Schedule: 9/80 – 9 hours Monday – Thursday, 8 hours every other Friday
Job Description:
The Welding Process Quality Engineers are responsible for ensuring that delivered products and/or services conform to contractual and the Company’s requirements by designing, implementing, evaluating and continually improving quality assurance and control methods and systems. They translate design drawings and contractual requirements into a comprehensive, understandable and functional quality plan; monitor and closely support manufacturing, inspection and supplier functions that relate to product quality; coordinate with the customer the establishment of government quality requirements and material review board activities; represent quality assurance in corrective action activities; and participate in audits or product evaluations to determine the effectiveness of the quality assurance program. These positions collaborate with engineering laboratory and production functions to ensure quality standards are in place.
The Welding Quality Process Engineer is responsible for ensuring that quality requirements are integrated and captured in various special processes utilized in the Canoga Park facility. This role necessitates a strong understanding of industry standards, internal command media and extensive practical experience to support development and deployment of best practices. The Senior QPE is expected to coordinate with internal and external customers to quickly resolve manufacturing issues and utilize their technical background to proactively drive process improvements. This position will have a heavy emphasis on welding and welding related support processes.
Essential Functions:
Functions as a lead in the review of failure investigation activities to ensure root cause is identified and mitigating activities are identified and implemented
Leads audit and inspection preparation, resolution of audit and inspection findings and liaises with auditing groups and inspectors through all stages of the audits
Coordinates communication with DCMA on quality issues, corrective action activities as well as advocacy for DCMA concerns
Coordinates quality participation in engineering milestone reviews and the related product life cycle
Provides leadership and participates in cause and corrective action activities, failure investigations, metrics creation and quality improvement projects
Ensures quality requirements are embedded into key manufacturing special processes, with a heavy emphasis on welding.
Provides leadership in the development and implementation of inspection plans that utilize Coordinate Measuring Machines (CMMs), Standard Measuring Inspection (SMI) equipment, quality tool and gage processes, sample inspection, NDT, special process certification controls, and Statistical Process Control (SPC) techniques
Participates in nonconforming material control and the Material Review Board (MRB) processes
Proactively analyzes manufacturing data to identify opportunities and implement process improvements
Independently manages quality projects, including coordination with cross functional team members, to ensure timely project completion.
Other responsibilities assigned by management as necessary.
Qualifications:
Bachelor’s Degree and minimum 6 years of prior relevant experience. Graduate Degree and a minimum of 4 years of prior related experience. In lieu of a degree, minimum of 10 years of prior related experience.
Knowledge of:
Applicable codes, rules and regulations related to the area of assignment
Quality engineering and mission assurance principles
Principles of quality planning and creating a quality plan
Failure investigation, root cause and corrective action processes
Nonconformance reporting and the Material Review Board (MRB) process
Quality management system standards
Qualification process and testing
Risk management process
ERP and Manufacturing Execution Systems (MES)
Geometric Dimensioning and Tolerancing (GD&T) techniques
Coordinate Measuring Machines (CMMs) and Standard Measuring Inspection (SMI) equipment
Applicable machine shop, weld, composite, propellant, electrical and assembly processes
Non-Destructive Test inspection processes
Dimensional, visual, sample and witness inspection processes
Tooling/gage processes
Special process certifications
Process Failure Modes and Effects Analysis (PFMEA)
Basic quality laboratory processes
Basic clean room practices and methods
Calibrations system requirements
Configuration management
Computer systems and applicable software programs such as Microsoft Office suite
Data mining quality management data techniques
Ability to:
Audit, interpret and evaluate data and processes
Use a variety of test, inspection and measurement equipment
Read and interpret blueprints and related specifications
Apply and interpret Geometric Dimensioning and Tolerancing (GD&T)
Operate effectively in a team environment
Conduct investigation, studies and research
Create process and program metrics to evaluate the quality health
Effectively communicate, both orally and in writing
Interface effectively with external customer counterparts
Deal with multiple tasks and deadlines set by management
Work safely without presenting a direct threat to self or others
Preferred Additional Skills:
AWS Certified Weld Inspector OR 5 years of hardware related experience with welding.
ASQ Certified Quality Engineer
Candidates supporting welding operations in an engineering capacity within an AS9100 QMS with limited quality experience are encouraged to apply.
In compliance with pay transparency requirements, the salary range for this role is $92,500 - $171,500. This is not a guarantee of compensation or salary, as final offer amount may vary based on factors including but not limited to experience and geographic location. L3Harris also offers a variety of benefits, including health and disability insurance, 401(k) match, flexible spending accounts, EAP, education assistance, parental leave, paid time off, and company-paid holidays. The specific programs and options available to an employee may vary depending on date of hire, schedule type, and the applicability of collective bargaining agreements.
L3Harris Technologies is proud to be an Affirmative Action/Equal Opportunity Employer. L3Harris is committed to treating all employees and applicants for employment with respect and dignity and maintaining a workplace that is free from unlawful discrimination. All applicants will be considered for employment without regard to race, color, religion, age, national origin, ancestry, ethnicity, gender (including pregnancy, childbirth, breastfeeding or other related medical conditions), gender identity, gender expression, sexual orientation, marital status, veteran status, disability, genetic information, citizenship status, characteristic or membership in any other group protected by federal, state or local laws. L3Harris maintains a drug-free workplace and performs pre-employment substance abuse testing and background checks, where permitted by law.