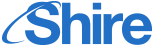
Job Information
Abbott Manufacturing Engineer/Quality Engineer in Clonmel, Ireland
Have you ever wanted to make a difference?
At Abbott, you will play a crucial role to help people live more fully at all stages of their lives. Abbott is a global healthcare leader and our portfolio of life-changing technologies spans the spectrum of healthcare, with leading businesses and products in diagnostics, medical devices, nutritional products and branded generic medicines. Our 113,000 colleagues have a daily impact on the life of people in more than 160 countries.
Abbott Ireland
In Ireland, Abbott employs over 6,000 people across ten sites. We currently have six manufacturing facilities located in Clonmel, Cootehill, Donegal, Longford and Sligo and a third-party manufacturing management operation in Sligo. Abbott also has commercial, support operations and shared services in Dublin and Galway. We have been making a difference in the lives of Irish people since 1946.
Vascular Division Clonmel
Abbott Vascular is one of the world's leading vascular care businesses. Abbott Vascular is uniquely focused on advancing the treatment of vascular disease and improving patient care by combining the latest medical device innovations with world-class pharmaceuticals, investing in research and development, and advancing medicine through training and education. Our broad line of vascular devices–which includes vessel closure, endovascular and coronary technologies–are used to treat vessel diseases of the heart, carotid arteries, and peripheral blood vessels. These vessel diseases can lead to heart attack, stroke, critical limb ischemia, and other serious vascular conditions.
We are currently looking for Manufacturing Engineers and Quality Engineers to join our modern site in Clonmel.
This is how you will make a difference:
As a Manufacturing Engineer, you will be responsible for engineering support of manufacturing operations, which will involve key engineering metric management and process optimization activities including Manufacturing Yield improvement, product quality monitoring, lean manufacturing design and material/equipment/process troubleshooting using continuous improvement tools and methodology. Working as part of the operations support team, the manufacturing engineer will liaise with operations, quality, R&D and materials & purchasing departments to ensure quality and efficient manufacturing operations.
Main responsibilities
Initiates and completes technical activities leading to new or improved products or process, for current programs, next generation programs and to meet strategic goals and objectives of the company.
Prepares reports, publishes, and makes presentations to communicate findings.
Analyses and solves problems from basic engineering principles, theories and concepts through to a wide range of complex and advanced problems which require novel and new innovative approaches or a major breakthrough in technology.
Understands engineering principles theories, concepts, practices and techniques.
Understands the business needs of the company, and has knowledge of the customer needs of our business.
Understands the business cycle and foresight of emerging technologies trends.
Cultivates internal and external network of resources to complete tasks. Serves as a resource in the selection orientation and training of new engineers and employees.
May lead a project team, determining goals and objectives for the projects.
Mentors employees by sharing technical expertise and providing feedback and guidance.
Interacts cross functionally and with internal and external customers.
Serves as a consultant for engineering or scientific interpretations and advice on significant matters.
Acts as a spokesperson to customers on business unit current and future capabilities.
Participates in validation activity. Role may vary between providing input to owning activities such as protocol/report writing and managing execution of validation activities.
Experience, Education and Skills Required - Manufacturing Engineer:
National Framework of Qualifications (NFQ) level 7 qualification in a relevant discipline.2+ years of related work experience, or an equivalent combination of education and work experience.
Basic technical knowledge of concepts, practices and procedures. Limited understanding of business unit/group function.
Learns to use professional concepts and company policies and procedures to solve routine problems.
Developing a network of internal resources to facilitate completion of tasks.
JOB DESCRIPTION:
About Abbott
Abbott is a global healthcare leader that helps people live more fully at all stages of life. Our portfolio of life-changing technologies spans the spectrum of healthcare, with leading businesses and products in diagnostics, medical devices, nutritionals and branded generic medicines. Our 109,000 colleagues serve people in more than 160 countries.
Abbott Ireland Vascular Division Clonmel
Abbott Vascular is one of the world's leading vascular care businesses. Abbott Vascular is uniquely focused on advancing the treatment of vascular disease and improving patient care by combining the latest medical device innovations with world-class pharmaceuticals, investing in research and development and advancing medicine through training and education.
Our broad line of vascular devices–which includes vessel closure, endovascular and coronary technologies–are used to treat vessel diseases of the heart, carotid arteries and peripheral blood vessels. These vessel diseases can lead to heart attack, stroke, critical limb ischemia and other serious vascular conditions.
Purpose Statement:
Provide Process/Quality Engineering support to manufacturing, helping to ensure delivery of highest quality product to the customer. Provide Process/Quality Engineering support to product development teams, helping to ensure development of highest quality new products.
Shift Role: 2-cycle shift (8-16:30 and 16:30-00:30)
Key Responsibilities - Quality Engineer:
Identifies manufacturing process defects (scrap, non-conforming material, customer complaints) by dispositioning non-conforming material, identifying primary root causes and suggesting corrective and preventative actions. May be responsible for querying and bounding data to support implementation of basic product stops.
Assists in development of product quality plans, documents and systems by providing input to product specifications, quality specifications, quality plans, risk analyses, Failure Mode Effect Analysis (FMEA) in conjunction with other product development team members. May be responsible for providing input to risk analyses and Failure Mode Effect Analysis’ (FMEAs).
Becomes skilled at using process monitoring systems by starting to identify critical process steps and applying basic methods to reduce process variation to reduce/eliminate the cause of defects.
Assists product/process improvement efforts (example, scrap, nonconforming product, customer complaints) by systematically gathering quality metric data based on previous program templates and by assisting in the appropriate analysis methods to enhance sustaining product design and new product development.
Becomes skilled at using quality tools and training materials by working with existing quality tools and training materials and by understanding evolution/history of tools in use.
Participates in validation activity. Role may vary between providing input to owning activities such as protocol/report writing and managing execution of validation activities.
Participates in corrective and preventive action activity.
Participates in Field Discrepancy Notification (FDN) investigations.
Education & Job Skills - Quality Engineer
(Education/ Experience) National Framework of Qualifications (NFQ) level 7 qualification in a relevant discipline. 2+ years of related work experience, or an equivalent combination of education and work experience.
(Technical/Business Knowledge (Job Skills)) Working technical knowledge and application of concepts, practices and procedures. General understanding of business unit/group function. Will perform this job in a quality system environment. Failure to adequately perform tasks can result in noncompliance with governmental regulations.
(Cognitive Skills) Works on problems of moderate scope where analysis of situations or data requires a review of identifiable factors. Exercises judgment within defined procedures and practices to determine appropriate action. Has a broad knowledge of technical alternatives and an understanding of their impact on the systems environment.
(Influence/Leadership) Cultivates a wide range of internal networks and begins to develop an extensive external network of resources to facilitate completion of tasks. May lead a project team of moderate scope. Provides guidance to less experienced staff. Acts as a mentor to lower level individual contributors. Influence exerted at peer level and occasionally at first levels of management.
(Planning/Organisation) Plans, organises, and prioritises own daily work routine to meet established schedule.
(Decision Making/Impact) Exercises authority and judgment within defined limits to determine appropriate action. Failure to achieve results or erroneous decisions or recommendations may cause delays in program schedules and may result in the allocation of additional resources.
(Supervision Provided) May provide limited work direction and guidance to exempt and/or skilled nonexempt levels of employees, may be asked to evaluate performance of and assist in career development planning for subordinates.
An Equal Opportunity Employer
Abbot welcomes and encourages diversity in our workforce.
We provide reasonable accommodation to qualified individuals with disabilities.
To request accommodation, please call 224-667-4913 or email corpjat@abbott.com