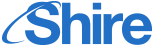
Job Information
Fujifilm Manufacturing Process Engineer II in College Station, Texas
Overview
The work we do at FDB has never been more important—and we are looking for talented candidates to join us. We are growing our locations, our capabilities, and our teams, and looking for passionate, mission-driven people like you who want to make a real difference in people’s lives. Join FDB and help create the next vaccine, cure, or gene therapy in partnership with some of the most innovative biopharma companies across the globe. We are proud to cultivate a culture that will fuel your passion, energy, and drive - what FDB call Genki.
College Station, Texas may be a small, university town, but the lively cultural scene and local amenities make it a great place for families as well as those who want the ease of small-town life and the convenience of living close to the vibrant pulse of big cities. Eighty-seven percent of Texas' population lives within a 180-mile radius, so we are in the center of it all in Texas. And our site is nestled in the hub of innovation, representing a source of pride for the area.
External US
Summary : The Manufacturing Process Engineer II is an integral part of the Manufacturing Technical Operations department located in College Station, Texas. This position will report directly to the Manager of Technical Operations, Manufacturing.
Works independently and with colleagues to provide expertise and assistance for the design, development, standardization, and maintenance of an operational biotechnology utilized to manufacture various proteins and other drug substances. This person would become the subject matter expert on core manufacturing and operational technologies for the manufacturing unit. Operational biotechnologies include 1. USP: Isolators and biosafety cabinets and their use in cell propagation, Cell Culture/Single Use Technology for adherent and suspension culture; 2. DSP: Dispensing and Mixing and Buffer Preparation, Chromatography, Tangential Flow Filtration, various filtration technologies, centrifugation, and Bulk Fill. This position will also create training programs and perform training for manufacturing technicians in the unit operation categories.
Essential Functions:
Develop and maintain equipment and unit operation standards and procedures utilizing the 4M (Man, Materials, Machinery, and Methods) approach, including:
(Man) Develop and deliver practical skill-building and training plans for a given operational technology to manufacturing technicians.
Collaborate with individuals and teams of technicians & managers on self-development plans.
Responsible for interfacing with internal/external technical experts and peers to maintain a broad knowledge of the technology and regulatory issues that impact the biopharmaceutical business, enabling technology options to be identified, evaluated and compared.
Responsible for specifying, purchasing, designing, qualifying, and handing over effective manufacturing systems, ensuring plant modifications have credible delivery plans.
Implement e-learning, video, classroom, and in-suite design and delivery as appropriate.
Take the lead in investigating and resolving events that arise from compliance issues.
Assist in identifying improvement to and managing change in technology transfer practices to deliver continuous improvements.
Create and maintain the technical training manuals and personnel certification process.
Develop and ensure training and skill-building activities align to site business requirements.
Assure local operational practice reflect local procedure and instruction.
Provide guidance and direction on cross-functional training initiatives.
(Materials) Understand process control and material inputs to ensure capable and acceptable process output.
- Ensure supplies are in place to execute water runs and Engineering Test Plans/Studies.
(Machinery) Understand technology operation capabilities, limits, and control strategies.
Review and/or Approve equipment qualification limits.
Review Calibration Tolerances and Approve Out of Tolerance Investigations
Coordinate validation, calibration, and PM completion of manufacturing lab equipment
Creation and or revision of recipes or methods for various platforms.
Represent the manufacturing unit for equipment purchase, new technology, and changes to equipment.
(Methods) Develop and maintain Technical Operational Manuals/Standard Operating Procedures/Work Instructions/Batch Records.
Lead operational technology standardization, standard batch templates, and instruction interfaces and lead continuous improvement for a given technology.
Assist in transferring and scaling new processes and technologies to the manufacturing plant, ensuring requirements for EHS and cGMP compliance.
Ensure procedures are in place to execute water runs and Engineering Test Plans/Studies
Interface with Process Development and Process Science to ensure a smooth transfer of processes into the manufacturing plant.
Develop and approve procedures and batch records.
Author URS (user requirement specification) documents
Ensure best practice operating methods are deployed and assist in resolving operational problems such as deviations, QIPs, CAPAs, change controls, etc.
Review and approve batch records, process validation protocols, process specifications, BOMs, campaign summary reports, and other documentation.
All other duties as may be assigned.
Required Skills & Abilities:
Excellent oral and written communication skills and interpersonal and organizational skills.
Strong leadership skills.
Ability to train others to perform to cGMP standards.
Proficient with Microsoft Office applications.
Good self-discipline and attention to detail; ability to work under minimal supervision.
Must have flexible work hours –willing to work outside of normally-scheduled hours, including opportunities for alternative shift hours and weekends as required.
Experience working in cleanroom environments under sterile or aseptic conditions; must have experience in engineering standards required for this type of operation.
Must have good planning skills and be willing to interface with and guide colleagues in many different roles and functions throughout the manufacturing facilities.
Working Conditions & Physical Requirements:
An employee must meet the physical demands described here to perform the essential functions of this job successfully. Reasonable accommodations may be made to enable individuals with disabilities to perform essential functions. While performing the duties of this job, the employee is regularly required to:
Experience prolonged standing, some bending, stooping, pushing, pulling, reaching above shoulders, and stretching.
Use hand-eye coordination and manual dexterity sufficient to operate a keyboard, photocopier, telephone, calculator, and other office equipment.
Lift up to 25 pounds frequently and up to 50 pounds occasionally.
Attendance is mandatory. This is a manufacturing support position. Work remotely is only allowed occasionally with previous coordination and management approval. (90% on the side; 10% from home).
This position requires being on-call or on-site during critical manufacturing activities.
Minimum Qualifications:
Bachelor’s degree in Science, Engineering, or other related field and two (2) years of biotech manufacturing experience;OR
Associate degree in Science, Engineering, or other related field and four (4) years of biotech manufacturing experience; OR
High School/GED with six (6) years of biotech manufacturing experience
All above must have two (2) years of GMP experience
Preferred Qualifications:
Previous Process Engineering experience.
Experience in developing training materials.
Experience conducting and evaluating training.
Experience with laboratory and or manufacturing instruments/equipment.
Previous leadership roles.
Join us! FDB is advancing tomorrow’s medicine, impassioning employees to chase the impossible and continually expand their potential. We are a company of emboldened goal seekers – driven by an innate desire to better ourselves, our families, our workplace, our company, our community, and the world at large.
We are an equal opportunity and affirmative action employer. All qualified applicants will receive consideration without regard to race, color, national origin, sex, gender identity, sexual orientation, religion, disability, protected veteran status or any other characteristic protected by applicable federal, state, or local law. If an accommodation to the application process is needed, please email FDBTHR@fujifilm.com or call 979-431-3500.
To all agencies: Please, no phone calls or emails to any employee of FUJIFILM about this requisition. All resumes submitted by search firms/employment agencies to any employee at FUJIFILM via-email, the internet or in any form and/or method will be deemed the sole property of FUJIFILM, unless such search firms/employment agencies were engaged by FUJIFILM for this requisition and a valid agreement with FUJIFILM is in place. In the event a candidate who was submitted outside of the FUJIFILM agency engagement process is hired, no fee or payment of any kind will be paid.
Job Locations US-TX-College Station
Posted Date 1 week ago (11/13/2024 4:40 PM)
Requisition ID 2024-32500
Category Manufacturing Science & Engineering
Company (Portal Searching) FUJIFILM Diosynth Biotechnologies