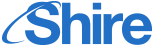
Job Information
Eaton Corporation Principal Manufacturing Engineer in Davenport, Iowa
Eaton’s IS AER MSD division is currently seeking a Principal Manufacturing Engineer. This position will be located at our Davenport, IA facility.
The Davenport facility has approximately 900 employees and is a leader in the design, development, manufacture and delivery of Aerospace life support and safety systems components and services to the global aftermarket and OEM markets.
The Principal Manufacturing Engineer will lead a team of manufacturing engineers to drive process improvement through designing, planning, and implementing innovative and best in class manufacturing processes and capital improvement projects. They will support day to day operations and will ensure that all customer expectations and deliveries are met.
The expected annual salary range for this role is $91500.03 - $134200.04 a year. This position is also eligible for a variable incentive program.
Please note the salary information shown above is a general guideline only. Salaries are based upon candidate skills, experience, and qualifications, as well as market and business considerations.
What you’ll do:
• Lead a team of manufacturing engineers to ensure that the capacity and capability of our manufacturing processes are best in class.
• Drive cost effective manufacturing using lean tools.
• Facilitate NPI process across multiple functions by acting as a liaison between Engineering and Operations through Production Readiness Reviews, Product Development design reviews, Integrated Product Teams and Cost Estimates.
• Use a structured, critical, analytical engineering approach to solve chronic, complex process and product problems.
• Develop and/or improve current processes, process documentation, and blueprint revisions and/or corrections utilizing the defined change control / engineering change request process.
• Work with Design Engineering and outside vendors to identify, evaluate, and incorporate new processes/technology into new and existing designs.
• Identify, justify, purchase and incorporate new capital equipment.
• Manage Manufacturing Bills Of Materials (MBOMs) and routing for new and existing products.
• Address and resolve issues arising from risks analysis, environmental conditions, and ergonomic evaluations.
• Conduct risks analysis, evaluates environmental conditions, and ergonomic evaluations for new, updated, or adjusted production processes.
• Ensure all processes and actions uphold the high standards of safety, quality, and cost of the product(s).
• Evaluate vendor capabilities from a manufacturing engineering process perspective.
Qualifications:
Required (Basic) Qualifications:
• Bachelor’s degree in Engineering from an accredited institution.
• Minimum of five (5) years manufacturing engineering experience.
• Minimum of two (2) years leading manufacturing engineering teams or projects.
• Must be legally authorized to work in the United States without company sponsorship, now or in the future.
• This position requires use of information or access to hardware which is subject to the International Traffic in Arms Regulations (ITAR). All applicants must be U.S. persons within the meaning of ITAR. ITAR defines a U.S. person as a U.S. Citizen, U.S. Permanent Resident (i.e. 'Green Card Holder'), Political Asylee, or Refugee.
• No relocation benefit is being offered for this position. Only candidates within a 70-mile radius of Davenport, IA will be considered. Active-Duty Military Service member candidates are exempt from the geographical area limitation.
Preferred Qualifications:
• Bachelor’s degree in Industrial Engineering, Industrial Technology, Mechanical Engineering, Manufacturing Engineering, or Aerospace Engineering from an accredited institution.
• Experience with following tools: Design for Manufacturability (DFM) practices, Statistical Process Control (SPC), Geometric Dimensioning and Tolerancing (GD&T), Process Failure Mode Analysis (PFMEA), Process Mapping, Root Cause and Corrective Action (RCCA) Process, Design of Experiments, ANOVA, Gage R & R.
• Manufacturing experience in a union environment.
• Experience with KPI (Key Performance Indicator) goals.
• Experience with Manufacturing Processes (Electrical, Chemical, and Mechanical Assembly, Fabrication, Welding, Paint, Solder, etc.).
• Experience with Change Control Board, and Engineering Change processes.
• Experience with AS9100, ISO9100, SAE, SME, ANSI, MIL-STD, Nadcap, BAC, IPC J-STD and other standards as related to International, Federal, State, Local, and Customer requirements.
• Experience with Enterprise Resource Programs (ERP), Material Requirements Planning (MRP), Capacity Resource Planning (CRP) such as SAP, Oracle.
• Experience with CAD software (PRO E, Creo, CATIA), CNC programming, PLC programming.
#LI-CB3
We are committed to ensuring equal employment opportunities for all job applicants and employees. Employment decisions are based upon job-related reasons regardless of an applicant's race, color, religion, sex, sexual orientation, gender identity, age, national origin, disability, marital status, genetic information, protected veteran status, or any other status protected by law.
Eaton considers qualified applicants regardless of criminal histories, consistent with local laws. To request a disability-related reasonable accommodation to assist you in your job search, application or interview process, please call us at 1-800-836-6345 to discuss your specific need. Only accommodation requests will be accepted by this phone number.
We know that good benefit programs are important to employees and their families. Eaton provides various Health and Welfare benefits as well as Retirement benefits, and several programs that provide for paid and unpaid time away from work. Click here (https://www.eaton.com/content/dam/eaton/company/careers/US%20Benefits%20updated%2010.24.22.pdf) for more detail: Eaton Benefits Overview. Please note that specific programs and options available to an employee may depend on eligibility factors such as geographic location, date of hire, and the applicability of collective bargaining agreements.