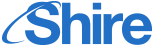
Job Information
J&J Family of Companies Main Assembly - Manufacturing Operator in Irving, Texas
Johnson & Johnson is currently seeking a Manufacturing Operator to join our Mentor LP located in Irving, TX.
At Johnson & Johnson, we believe health is everything. Our strength in healthcare innovation empowers us to build a world where complex diseases are prevented, treated, and cured, where treatments are smarter and less invasive, and solutions are personal. Through our expertise in Innovative Medicine and MedTech, we are uniquely positioned to innovate across the full spectrum of healthcare solutions today to deliver the breakthroughs of tomorrow, and profoundly impact health for humanity. Learn more at https://www.jnj.com/.
KEY RESPONSIBILITIES:
Under limited supervision and in accordance with all applicable federal, state and local laws/regulations and Corporate Johnson & Johnson, procedures and guidelines, this position
Assembles various materials into subassemblies or finished products using appropriate tools and equipment. Interprets instructions and specifications and uses to set up equipment. Maintains accurate records/documentation related to work in progress and quality checks. Checks products on assembly line to confirm that they are accurately assembled and removes defective products. Cleans and maintains equipment as needed. Works with production supervisor and/or engineers to resolve line issues. Troubleshoots minor production problems. Notifies supervisor of maintenance and/or repairs needed on equipment.
Performs in process quality checks on sub-assemblies and finished products.
Operates small equipment, cutter machines, jigs, filling equipment, and assembly fixtures and standard measuring instruments.
Performs assembly of molded rubber part sub-assemblies.
Monitors and responds to equipment and process issues that may lead to non-compliance.
Accountable for adhering to and implementing all quality and safety guidelines.
Identifies and elevates all immediate and potential quality, safety, or environmental issues (material, procedure, and process) as observed.
Inspects assemblies and sub-assemblies devices.
Reviews device records, follow established procedures, and prepares documentation as the need arises.
Must maintain good manufacturing and documentation practices in accordance to procedures outlined according to cGMP.
Flexibility to cross train to other departments according to business needs. Provide training to new employees or other team members as requested. Maintains an updated and current training record and adheres to training timelines.
Report unsafe practices/conditions to shift/team leader.
Identify continuous improvement opportunities for process and equipment. Helps to meet daily efficiencies by focused approach to performing tasks compliantly and safely according to procedure/process.
Responsible for ensuring personal and Company compliance with all Federal, State, local and Company regulations, policies, and procedures
Demonstrate independent understanding and application of core GMP fundamentals, including but not limited to: Data Integrity (DI), Good Manufacturing Practices (GMP), and Good Documentation Practices (GDPs).
There is an internal pre-identified candidate for consideration. However, all applications will still be reviewed.
Qualifications
There is an internal pre-identified candidate for consideration. However, all applications will still be reviewed.
Qualifications:
A minimum of a High School diploma, G.E.D. or equivalent required.
A minimum of 2 years of experience in a machine shop or production line environment is preferred.
Experience working in a Medical Device manufacturing environment preferred.
Experience working in a Good Manufacturing Practice (GMP) or other regulated environment preferred.
The ability to read manufacturing blueprints is required.
The ability to follow work instructions is required.
Basic computer skills required.
Must be able to communicate (read, write, speak) effectively in English is required.
The ability to perform fine manipulation procedures using scissors and tweezers is required.
The ability to lift and/or move up to 20 pounds is required. The ability to stand and/or walk up to 80% of the time is required.
The ability to work 1st/2nd shift is required. The ability to work occasional overtime and weekends is required.
Johnson & Johnson is an Affirmative Action and Equal Opportunity Employer. All qualified applicants will receive consideration for employment without regard to race, color, religion, sex, sexual orientation, gender identity, age, national origin, or protected veteran status and will not be discriminated against on the basis of disability.
For more information on how we support the whole health of our employees throughout their wellness, career and life journey, please visit www.careers.jnj.com.