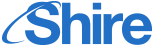
Job Information
Eaton Corporation Lean Coordinator in Juarez, Mexico
Eaton’s ES AMER ARS division is currently seeking a Lean Coordinator.
What you’ll do:
PRIMARY FUNCTION:
Responsible to drive efforts to make the Eaton Business System and Eaton Lean Six Sigma the primary continuous improvement programs to identify, plan, and execute Operational Excellence initiatives. This position leads, facilitates and drives Continuous Improvement initiatives to improve process capability, reduce waste and eliminate defects. Achieve measurable improvements by managing multiple Lean / Continuous Improvement projects and working with employees to implement process changes to improve efficiencies, reduce cost, improve quality and improve delivery performance.
ESSENTIAL FUNCTIONS:
• Coordinate ELSS teams and ELSS 8 tools ‘champions to develop and execute strategic plans for continuous improvement in support of the Plant’s KOF (Key Operating Factors).
• Lead plant through Value Stream Mapping and Business Process Improvements in line with the Annual/Mid- Year Strategic Planning process. Act as VSM Tool Leader.
• Lead, coach and facilitate Continuous Improvement Events such as Kaizens, Six Sigma Projects in on time delivery metrics while reducing cost, inventory and lead time.
• Contributes in the identification of cost-out projects, keeping a healthy project deck in terms of achieving Cost-Out Plant’s goals.
• Implement effective measurement tools associated with continuous improvement and cost out, track and communicate this metrics Plant wide and to the Electrical Sector - Americas. including the ELSS Self-Assessments and the OpA Operations Assessment
• Conduct training needs assessment associated with ELSS Competencies and conduct training as required driving overall Lean Culture.
• Coordinate Gemba Walks; schedule, teams and action items to keep Leadership Team engaged in the process.
• Drive best practice sharing along with internal and external benchmarking.
• Work as required with other functional areas to ensure lean is deployed.
Qualifications:
• Bachelor’s Degree in Engineering required.
• Experience in Lean Manufacturing systems and in process improvements.
• Strong analytical skills and understanding of problem-solving tools/methods and goal setting process required.
• ASQ Certified Quality Engineer
• Six Sigma Black Belt and previous EBE experience preferred.
• Strong communication and facilitation skills along with an innovative mindset required.
• Must have the ability to effectively communicate across all levels of the organization.
• Must have the ability to work through others to get results (building relationships, rapport, and influencing).
• Computer skills and the use of Microsoft Office tools and Minitab are a necessity.
ADDITIONAL INFORMATION:
ISO 14001: 2015
• Ensure that operational controls applicable to your areas are carried out.
• Follow up on the questions of the staff in charge, referring to the S.A.A.
• Support compliance and monitoring of environmental and Safety policy.
• Contribute to the achievement of Environmental & Safety Goals
• Support to maintain the S.A.A. for the care of the Environment.
• Carry out the activities established in the Methods and Procedures of the S.A.A.
• Understand the impacts of Environmental Aspects.
• Carry out the provisions of the Operational Controls.
We are committed to ensuring equal employment opportunities for job applicants and employees. Our recruitment processes use balanced selection criteria and avoid unlawful discrimination against applicants on the basis of their age, colour, disability, marital status, national origin, gender, gender identity, genetic information, race or racial origin, religion, sexual orientation or any other status protected or required by law.