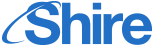
Job Information
The Coca-Cola Company Supply Chain & Inventory Analyst in Manzini, Swaziland
B. JOB SUMMARY: Describe the Purpose of your Job. (What and how do you do and why do you do it?)
CPS (Commercial Products Supply) is a key part of the Advantaged Supply Chain of the Technical Function of The Coca-Cola Company. CPS manufactures concentrates and beverage bases for sale to bottling partners all over the world. This global organization manages a network of 19 manufacturing plants in 18 different countries along with 2 office locations (Atlanta, USA & Drogheda, Ireland). CPS also manages complex additional materials supply chains (e.g. juice, coffee, tea, milk, etc.) on behalf of bottling partners.
The Conco Supply Chain & Inventory Analyst will be a key member of the Plant Planning & Logistics team of Eswatini and will be responsible for end-to-end Inventory Management to ensure adequate monitoring of inventory KPI's such as Weeks of stock (WOS), Age of Stock (AOS), stock turn over, Inventory movements in manufacturing and warehouse processes as well as product freshness. The Supply Chain & Inventory Analyst will be responsible for all Inventory processes including driving the monthly MRB meeting with cross functional teams, among other routines.
This role oversees inventory analysis ensuring proper inventory levels and managing inventory at risk while also ensuring the plant has updated planning parameters which reflect the desired inventory policy for each SKU or products/ingredients group. The Supply Chain & Inventory Analyst will collaborate with cross functional teams within the plant and leverage best practices across The Coca-Cola System.
This role will also be responsible for monitoring the products freshness to ensure that products are available for customer orders with adequate shelf life.
C. KEY DUTIES/RESPONSIBILITIES:
Briefly describe the primary duties/responsibilities of the job in bullet points. Please list these duties in order of importance and include the percentage of time spent or required for each activity.
GENERAL SUPPLY CHAIN ANALYTICS:
To run end to end Supply Chain analytics and reports to drive Collaboration with internal and external subject matter experts to resolve problems and implement improvements in the supply chain.
To actively partner with various business stakeholders in Logistics, Supply Planning, Warehouse, and all Supply chain workstreams to drive efficiency through data visualization and analytics, thereby enabling speedy insights for agile decision making.
INVENTORY POLICY MANAGEMENT:
Collaborate with Planning and Customer Services teams to develop a written inventory policy for all F.G SKU's whether at SKU level or Product Group level, ensure that this policy is reviewed and updated frequently, and any change is reflected in SAP planning parameters with clear business rationale.
Monitoring the Finished Goods WOS every week and identify the top SKU's per MRP controller with high WOS value to be analyzed by Master Schedulers vs. inventory policy and ensure there is a clear narrative and corrective actions in place.
Monitoring the Ingredients WOS every week and identify the top 10 SKU's per MRP controller with high WOS value to be analyzed by Vendor Schedulers vs. inventory policy and ensure there is a clear narrative and corrective actions in place.
AGE OF STOCK MANAGEMENT:
Monitoring the Age of Stock (AOS) report for ingredients and F.G every week and identify the missing information in SAP to be shared with the owners (Customer Management for Finished Goods, Master Schedulers for BCH and Material Analysts for Ingredients and packaging materials).
Follow up with all stakeholders to submit the missing information of AOS before the next report run.
Maintaining the governance of AOS routines through measuring and analyzing the conformance to standard (% of missing information in AOS report, % of actions completion on time, Cost avoidance in USD, etc.).
Responsible for lead the Age of Stock sessions on a weekly basis and share the summary of High/Medium risks with the stake holders (Finance, Customer Management, Planning and Materials Management) and agree on the required actions to mitigate those risks.
Proactively identify and evaluate all finished products at risk (less 50% of remaining shelf life) to avoid obsolescence and to effectively manage inventory, to minimize negative financial impact across the total supply chain.
MONTHLY MRB ROUTINES:
Responsible for maintaining the MRB routine to measure plants inventory losses driven by CPS activities and follow up with relevant functions on the execution of MRB actions. As well as measure the plant inventory losses driven by a decision made by a BU or Bottler and follow up with CRM and Finance on provisions submission and approvals are obtained from the relevant BU's.
Responsible for preparing and sharing the list of materials ready for destruction every month with the key stakeholders (QSE, Finance & Warehouse) and follow up on the destruction report issuance and approvals. This shall include monitoring all block stock status and processes.
Responsible for write off nonconforming items after ensuring all process steps and supporting documents were completed.
Responsible to audit Inventory processes compliance and monitor Inventory risk on an ongoing basis while driving mitigation action plans cross functionally.
Apply OE tools and process Improvement methods to drive success across inventory management portfolio in the plant.
OPERATING UNIT, CUSTOMER, SUPPLIER ENGAGEMENTS:
Work with Product Portfolio teams in managing depletion plans and Product life cycle.
Monthly reporting and engagement with OU's and Customers on inventory risks to drive mitigations.
KPI AND REPORTING:
Reporting the plant Inventory KPI's for Ingredients and FG on an ongoing basis with trend charts and supported by narrative for off-track records and clear corrective actions with assigned owner/s for each action.
Responsible to drive Inventory management improvements to impact the system positively throughout the plant and supply chain teams.
Prepare Monthly Inventory reports for Operating Units, Key Customers etc.
ADHOC ITEMS
Responsible to execute related tasks as assigned from time to time including interphase with Master scheduling and Material Management teams.
Build operational and tactical capabilities through hands-on collaborative work and training programs.
Act as back up resource for Master scheduling
COMPLIANCE & GOVERNANCE:
Ensure that all activities are carried out in a way supporting the Company requirements such as KORE, SOX and all other local/system/international applicable requirements and regulations.
Routinely audit in process inventory movements to drive process compliance with cross functional teams in the plant.
OPERATIONAL EXCELLENCE:
- Ensure operational excellence approach is embedded and drive improvements of processes for the plant and Operating Units.
Safety Standards
Cooperate and follow instructions given by the employer, Commissioner of Labor, Inspector or any other person lawfully authorized to give such instructions in keeping the working conditions safe and without risk to health and injury in the field of that activity.
Use, any means, appliance, equipment or other safety devise for securing safety and health as provided by the employer for use and protection of the employee or property in any process a per the instructions given by the employer or any person lawfully authorized to do so.
Report to the employer (Conco Leadership Team) any situation as soon as it becomes unsafe or unhealthy, or where an accident occurs report such accident to the employer or supervisor responsible for maintaining a high EOHS (Environment Occupational Health and Safety) standard to protect their own health and safety and that of others.
Responsible to Follow and adhere to all EOSH policies and procedures.
Responsible to adhere to all applicable standards as communicated by the business
Immediate reporting all hazards, unsafe acts, unsafe conditions, and incidents.
D. FINANCIAL/ JOB SCOPE: Identify quantitative factors for your job, such as volume, annual budget, customer contacts (e.g., # of bottlers, customers, etc.), and other major indicators of the scope and complexity of your job.
Volume: over (4.6M SUN, 16M PDR)
Inventory ($): Average inventory value 70M.
# Brands/Products: over 252 different products formulas
# Product Launches Annually: 80 - 100 products
# Currencies: 4
# Bottlers (Customers) Managed: Supplied to over 50 customers in over 20 countries
E. ORGANIZATION IMPACT/ INFLUENCE: Indicate the nature and level of your contacts within and outside the Company, as well as the nature and purpose of the interaction.
This role reports directly to the plant Senior Manager, Planning and Logistics (Daily interaction).
Ongoing collaboration with cross functional team to maintain the inventory management routines (Planning, CM, MM, QSE, Warehouse, Logistics, Production, Finance, etc.)
All Functional Tactical Managers (Through the Inventory management routines).
F. SUPERVISORY RESPONSIBILITIES : List the number, if any, and type (full-time, part-time, contract) of your direct reports; indicate the extent of your involvement in supervision including hiring, conducting performance reviews, and terminations as well as team leadership, coordination of work assignments and other indirect supervision. Please attach a copy of your current organization chart, if available .
This role is an individual contributor. However, it requires certain leadership and influential skills to lead the inventory management routines and engage effectively with cross functional teams, Virtual teams, and management. This role also supports with data analytics and reports enabling key business decision-making.
G. RELATED JOB REQUIREMENTS/ QUALIFICATIONS: List the competencies needed to successfully perform your job, including the number of years and type of previous work experience. Please do not describe your own skills and experience, rather it should be the minimum amount required to perform the job.
- Type of previous work experience required:
Supply chain, preferably in food Manufacturing, Engineering, Finance, Business Administration, Data Science, Information Technology.
- Years of previous work experience required: 5+ years
Functional Competencies Required:
Previous experience in supply chain roles within CPS or equivalent organization
Business acumen, understanding of the KO System and Finance (P&L)
Strong interpersonal skills and experience in working within cross functional teams
Excellent Advanced analytical skills
Data Science, Programming
Excellent English spoken and written skills
SAP experience
Advanced level MS Excel and Power Point experience, PowerBI
Excellent organization, time management and follow-up skills
H. EDUCATIONAL REQUIREMENTS : Indicate the minimum education level required to perform the job.
Minimum education level required to perform this job:
Tertiary Bachelor's Degree in Supply Chain, Business Administration, Economics, Statistical Analysis, Engineering, Information Technology or Equivalent qualification.
An MBA would be an added advantage.
I. CULTURAL DIVERSITY: Please describe any language, ethnic or culture differences you face in your job. List any supervisory or Company spokesperson responsibilities you may have
- This role needs excellent interpersonal skills and very well-developed cultural awareness skills. Fluent written and spoken English is important as well as strong communication skills, as interacting with contacts from other concentrate plants and locations around the world (Asia, Europe, Africa, Latin America and United States) could be required.
J. ANALYSIS : Describe the types of problems you must solve to successfully perform your job. Is the process well defined, or must you develop new approaches to solve these problems?
Understand the end-to-end Supply Chain to propose solutions that will drive cost efficiency, deliver value, and create business opportunities
Uses of Information and Data - uses information in an effective and timely manner to resolve inventory problems.
Problem solving (assessment/solution) - uses a disciplined approach to define problems, identify root causes, generate solutions and choose the best solution; recognizes trends; identifies underlying issues.
Continuously seeking for improvement opportunities including the automation of work.
K. JUDGEMENT AND DECISION MAKING : Describe the nature and impact of decisions required in your job. Distinguish between recommendations you make to someone else and decisions where you have final authority. Indicate your involvement (if any) with ABP and OBP development and execution.
Recommendations of inventory levels for finished goods and ingredients.
Finished goods and ingredients freshness.
Write-off mitigations and Materials destruction
Materials shelf-life extension
FG reformulation
We are an Equal Opportunity Employer and do not discriminate against any employee or applicant for employment because of race, color, sex, age, national origin, religion, sexual orientation, gender identity and/or expression, status as a veteran, and basis of disability or any other federal, state or local protected class.