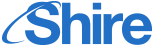
Job Information
The Sherwin-Williams Company Maintenance Coordinator in Massillon, Ohio
This position is primarily responsible for purchasing non-raw material parts, supplies and services for the facility. This position is critical to determining and maintaining appropriate minimum and maximum inventory levels using eAM system and economic order quantities, tracking spending, obtaining competitive pricing and identifying opportunities for improvement and implementing ideas. This position is responsible for contracted services including HVAC, compressed air system, forklift, and landscaping, including obtaining bids, negotiating annual contracts, and the coordination of repairs and preventative maintenance tasks. This position also handles the management of all permitting for various maintenance and engineering related tasks. Additional Information: 1st Shift - Monday - Friday 7:00a.m. - 3:30p.m. This position is also eligible for bonus based on performance and subject to the terms of the Company's applicable plans. This position is eligible for health benefits, such as medical, dental and vision coverage, Flexible Spending Accounts (FSAs), disability coverage, security, retirement and saving benefits, and more. Additional benefits include a generous time away from work package, including personal leave, paid parental leave, medical leave, vacation, holidays, among other benefits. For more information about our benefits, visit http://www.myswbenefits.com/. Secure competitive pricing on all non-raw material items and all contracted services purchased for the Plant. Prepare materials in advance of PM or work orders. Receive all incoming orders and ensure the quantity of the items received are correct and that all required documentation is in place prior to invoices being approved for payment. Maintain records of permits issued, safety and fire inspection report records, and ensure this work is scheduled on a timely basis, as well as ensure all inspections are up to date on a monthly and annual basis. Maintain accurate inventory levels at all times. Including a correct min/max level to ensure all lead times are met for parts orders, so that effective inventories are never depleted to the point of negatively affecting production or maintenance activities. Provides input in creating preventive maintenance activates using Failure Mode Effects Analysis, manufacturers manuals, and previous experiences. Participates in daily maintenance planning meetings to help establish priorities and deadlines for the department. Key participant in Site's Reliability Excellence Certification steps. Assists with the development of the department's annual budget. Maintains the stock room (adequate levels of repair parts and production supplies, janitorial, etc.), Ensuring all parts are received, inventoried, and properly located. Maintains inventory of all parts in eAM system. Contacts vendors for quotes and availability of parts and equipment. Assist in scheduling work and entering WO's in eAM Ensures that maintenance staff is notified when orders are received. Coordinates with maintenance staff to ensure that the proper parts are ordered and received in a timely manner. Supports departments and site initiatives such as Reliability Excellence, Sustainability, Housekeeping Excellence, Continuous Improvement, etc. Maintains records for all assets and associated BOM's in eAM. Minimum Requirements: Must be at least eighteen (18) years of age Must be legally authorized to work in the country of employment without needing sponsorship for employment work visa status now or in the future Must have ownership of the Rx metrics and Interrogating the Rx data to identify opportunities for Maintenance Improvements Must have working knowledge of environmental regulations Must have experience of Computer Maintenance Management Systems Preferred Qualifications: Have at least equivalent experience leading a maintenance te