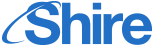
Job Information
Veolia North America Senior Reliability Engineer in Milwaukee, Wisconsin
Company Description
About Veolia North America
A subsidiary of Veolia Group, Veolia North America (VNA) offers a full spectrum of water, waste and energy management services, including water, and wastewater treatment, commercial and hazardous waste collection and disposal, energy consulting and resource recovery. VNA helps commercial, industrial, healthcare, higher education, and municipality customers throughout North America. Headquartered in Boston, Mass., Veolia North America has approximately 10,000 employees working at more than 350 locations across the continent. Please visit our website www.veolianorthamerica.com.
Job Description
BENEFITS
Veolia's comprehensive benefits package includes paid time off policies, as well as health, dental and vision insurance. In addition, employees are also entitled to participate in an employer sponsored 401(k) plan, to save for retirement. Pay and benefits for employees represented by a union are outlined in their collective bargaining agreement.
Position Purpose:
The Senior Reliability Engineer will support and lead various maintenance and reliability improvement initiatives. Veolia strategic sites across North America. (Middle, Middle West, West).
The key objective of these sites is to improve safety, reliability, and plant uptime by applying the most cost-effective maintenance strategies using Reliability Centered Maintenance (RCM), preventing recurring failures using Root Cause Analysis, and optimizing other processes related to maintaining these sites.
Primary Duties/Responsibilities:
Facilitates RCM analyses across simple to very complex systems.
Lead implementing maintenance and reliability strategies into Veolia's corporate computerized maintenance management system (CMMS).
Propose the identification and application of maintenance and reliability best practices.
Develop a working understanding of predictive technologies, vibration analysis, ultrasonic analysis, thermography, PdMA, oil analysis, corrosion detection, dissolved gas analysis, etc.
Lead the lubrication program effectiveness and the hydraulics improvement plan.
As required, provide training and lead root cause failure analysis (RCFA) and RCM.
Develop asset registers and hierarchies.
Conduct equipment condition assessments and Risk Performance Analyses.
Complete equipment criticality analysis.
Conduct root cause failure analyses (Cause Mapping).
Develop critical spare parts strategies.
Develop Preventive Maintenance Optimization activities.
Conduct Asset critical spare parts analysis and inventory management.
Work closely with Maintenance and Engineering, Operations Managers, Supervisors, and Planners to close reliability gaps, identify bad actors, and identify further improvement opportunities.
Assist by implementing computerized maintenance management systems.
Driving the development and resolution of top failure causes identified in reliability reports.
Qualifications
Education/Experience/Background:
BS degree in engineering (preferred, mechanical, electrical, chemical).
Min 5+ years of experience as a Maintenance Engineer, Manager or Supervisor, or as a Reliability Engineer.
Knowledge/Skills/Abilities:
Motivated and dynamic person with the ability to work independently and as part of a team.
Technically oriented (engineering focus).
Resourceful and proactive.
Good interpersonal skills - Self Motivated and Self-disciplined.
Skilled in CAD, Microsoft Office, Excel, Word, and PowerPoint, a must.
Good Communication skills.
Good listening and interpretation skills; speaks and writes effectively; reads and comprehends drawings, graphs, and charts.
Comfortable communicating at all levels of the organization.
Think systematically/methodically - logically to evaluate situations, solve problems, and make decisions. Pays attention to detail.
Computer literate - possesses good computer skills, i.e., MS Word, MS Excel, Google Docs, Google Sheets, etc.
Preferred Vibrations Institute Certification (Level I, II).
Preferred STLE (Society of Tribologist and Lubrication Engineers).
Possess strong working knowledge of VAMs or other CMMS and good command of MS Excel, MS Project, or similar.
Exposure to Lean Concepts, Reliability, layout design, cost/benefit analysis, labor productivity analysis (time studies, standardized work), and safety/ergonomic/human factors.
Data analyst and new processes developer/adapter.
Self-starter. Strong evidence of driving goals with minimal day-to-day supervision.
Required Certification/Licenses/Training:
Certified Maintenance and Reliability Professional (or similar), i.e., CMRP, CRL, ASQ, STLE.
Project Management Professional PMP.
Physical Requirements:
Travel (30 - 50%)
Professional business atmosphere.
Commitment to quality and the motivation and ability to work well in a team environment required.
Ability to multi-task in a fast-paced environment.
Occasionally walks around the office to printers, copy and fax machines.
Constantly sits while working at the computer.
Additional Information
We are an Equal Opportunity Employer! All qualified applicants will receive consideration for employment without regard to race, color, religion, sex, sexual orientation, gender identity, national origin, disability or protected veteran status.
Disclaimer: The salary, other compensation, and benefits information is accurate as of the date of this posting. The Company reserves the right to modify this information at any time, subject to applicable law.
Job Location