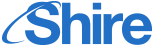
Job Information
JBS USA FAB QA SUPERVISOR in Plainwell, Michigan
About JBS
JBS began in 1953 as a small, family-owned company in Brazil. We have continued to steadily grow and are now the largest animal protein processor in the world. Though our business has grown, our family values remain our foundation. We seek to hire dedicated individuals who are committed to learning and share our desire to be the best. At JBS, our team members are our most important asset and feeding the world is our greatest goal. The Plainwell facility began operations in 1918 under the Murray Packing company. In the 1960's, it was acquired by Murco and in 1998 by Packerland. In 2000, Packerland was acquired by Smithfield. In 2010, the facility joined the JBS USA family.
Plainwell is the only JBS plant with Modified Atmospheric Packaging (MAP), a packaging process that changes oxygen levels to extend shelf-life. The MAP process is a part of the Plainwell ground beef operation. Plainwell is also one of the few plants that produces ground beef patties. Over one million lbs. (450,000 kg) of beef are produced each day. The Plainwell facility produces biogas in an anaerobic lagoon and uses it in place of natural gas to heat a portion of the water used in the plant. The facility was recognized by the American Meat Institute as a Tier 3 facility for its accomplishments with ISO 14001. Plainwell recently built a $31 million distribution center (85,000 ft²) with a 55,000 box capacity.
Opportunities
Investing in our people is a large part of the reason why success at JBS is so achievable. Working in operations gives you the opportunity to contribute to the very core of our business: producing the highest quality products for families around the globe. At the JBS operations facilities, we offer career growth opportunities for people with all kinds of interests and backgrounds who are interested in working in a fast-paced, hands-on environment. Additionally, opportunities for those who enjoy working within the production environment and are excited about both leading a team and ensuring we are producing a top quality, safe product for families across the globe.
Benefits
JBS® values the people who make our company a success. We want to be sure our team members know just how much we appreciate their dedication by ensuring they love working with us. As part of our total compensation package, JBS® and offers comprehensive employee benefits designed to meet the healthcare and financial goals of our team members and their families today, tomorrow and in the future.
DESCRIPTION SUMMARY
Assists leading the plant in assessing food quality and safety and other initiatives to improve products and processes related to quality, food safety and consistency. As a key member of the plant quality management team, the QA Supervisor assists the plant quality manager in providing quality and food safety leadership to employees. Participates in/leads projects to improve plant quality and food safety performance.
PRINCIPLE DUTIES AND RESPONSIBILITIES
The Quality Supervisor has the primary responsibility of maintaining and assisting in implementation of the food safety systems of the plant. These systems include but are not limited to the plant’s HACCP, SSOP and prerequisite programs to ensure compliance with all regulatory requirements for the production of safe and wholesome food.
Participates in the development and implementation of programs, policies, procedures, and work instructions for quality and food safety assessment and improvement.
Makes recommendations and decisions involving food safety and quality issues having significant potential business impact to corporate and plant management.
Trains, develops, and manages Quality Technicians. Responsible for the Quality Technicians' day to day activities.
Coordinates plant quality and food safety audits (internal and third party).
Works with plant management team to develop corrective action plans and communicates plans to QA and Plant Manager.
Recommends and /or develops orientation and training programs for quality, food safety, and GMP training.
Prepares monthly summary reports of key quality metrics, including issues and progress.
Advises plant on quality and food safety implications of changes in product, processing, or facility design.
Ensures compliance to quality, food safety, 5S, OSHA, and HAACP support programs.
Assures conformity to all company, customer, and government standards.
Responsible for ensuring appropriate product disposition for products produced or returned to this facility. Supporting and ensuring compliance of GFSI standards. Responsible for ensuring appropriate product disposition for products produced or returned to this facility. Supporting and ensuring compliance of GFSI standards.
Oversee monitoring, verification, and validation activities to ensure that all products leaving the facility(s) meet Food Safety and Quality standards.
EXPECTATIONS – all Team Members
Observe & enforce all company personnel, quality, safety, and food safety policies.
Maintains a positive work atmosphere by acting and communicating in a manner so that you work effectively and cooperatively with customers, clients, coworkers, and leadership teams.
Participates in process improvement and problem solving utilizing continuous improvement and rational thinking methodologies such as Six Sigma
KNOWLEDGE, SKILLS and ABILITIES
Bachelor’s degree (B.A.) from four-year college or university in Food Technology, Agricultural Business, Animal Science or a related field; or one to two years related experience and/or training; or equivalent combination of education and experience.
Considerable knowledge of Quality Services.
Considerable knowledge of supervisory management practices and principles
Considerable skill in communication skill.
Strong understanding of Meat processing, USDA, FSIS regulations, Food Safety and Quality Assurance standards and a commitment to food safety and quality.
Preferred HACCP and GFSI Certification
EOE/ Vets/ Disability