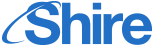
Job Information
Spirit AeroSystems Manufacturing Engineer in Prestwick, United Kingdom
Overview
Spirit AeroSystems designs and builds aerostructures for both commercial and defense customers. With headquarters in Wichita, Kansas, Spirit operates sites in the U.S., U.K., France and Malaysia. The company's core products include fuselages, pylons, nacelles and wing components for the world's premier aircraft. Spirit AeroSystems focuses on affordable, innovative composite and aluminum manufacturing solutions to support customers around the globe.
Role Purpose
Accountable for the management and development of accurate “Bills of Materials” maintained within the Enterprise Resource Planning System. Ensure that valid Engineering Processes are deployed within the manufacturing process and effectively detailed within the process routing to satisfy requirements of the business MRPII disciplines. Manage the formal Engineering Changes communicated and agreed with the customer and valid agreed internal changes. Deploy the Continuous Improvement toolset to enable productivity and product quality improvements to be implemented in support of business and customer requirements both internal and within the supply chain. Accountable for the Translation of Design Data (For example CAD/CATIA) and specifications into clear and concise work instructions for manufacturing products to customer and regulatory authority requirements.
Manufacturing Engineer
Salary: From £36,013 to £39,679
This opportunity, based at our Prestwick site offers:
37 hour working week (half day Friday)
Shift premiums up to 33%, where applicable
Overtime at time and a half, where applicable
33 days holiday per year, rising with service
Annual Bonus related to company performance
Defined contribution pension scheme (default contributions; 4% employee and 8% employer)
Virtual GP Service 365 days per year
Employee Assistance Program
A wide range of flexible benefits
Death in service payment (default 4 times basic salary)
Professional development and growth
Free car parking
And more!! (https://spiritaero.icims.com/icims2/servlet/icims2?module=AppInert&action=download&id=187171&hashed=1809974432)
Responsibilities
Responsible for the translation of Design Engineering data and specifications into clear and concise work instructions for manufacturing assemblies or product to customer and regulatory authority requirements.
Accountable for the maintenance and development of suppliers/conditions of supply.
Responsible for supporting Continuous Improvement to achieve significant productivity and quality improvements by:
Analysing and eliminating waste (seven wastes).
Developing and implementing production smoothing methods and Kanban systems.
Identifying and implementing methods to reduce set-up and overall cycle times.
Effective use of problem solving tools and techniques.
Responsible for the definition of hard to satisfy quality standards and optimise long term manufacturing costs.
Responsible for manipulating CAD data to support work activities when required.
Support the MRB process by providing engineering instructions relating to rework, scrap and future prevention of non-conforming products.
Implement visible control and business support systems in order to demonstrate effective management and control.
Liaising with operators, design and regulatory authorities to ensure product integrity and compliance.
Responsible for checking and acceptance of new and modified design models and drawings as approved signatories.
Responsible for provision of engineering/manufacturing support to external customers and contractors.
Responsible for the creation, maintenance and auditing of Engineering processes.
Assisting with product audits, identifying and implementing corrective actions.
Assisting with the close out of customer non-conformances.
Work closely with Design to identify and implement cost reduction initiatives and quality improvements.
Qualifications
Knowledge, Skills and Experience
Preferably be qualified to HNC level or equivalent in a related discipline.
Have 2 years relevant engineering experience within a Manufacturing Engineering environment.
Good communication skills – interface with customers and suppliers.
Knowledge of engineering systems and the ability to deploy the Continuous Improvement Toolset – Seven Wastes etc.
Awareness of drawings and systems as applied within our major customers such as Boeing and Airbus.
A good working knowledge of Microsoft Packages – Word, PowerPoint, Excel and Access.
Decision Making Authority
Guidance is typically available from established policies or from related procedures. In addition guidance is also available from well defined procedures (what to do, not how to do it).
Work is reviewed from time to time by the Senior Engineer/Team Leader. Only unusual problems/issues are referred to line manager and /or more experienced staff.
Decisions which affect their own job seldom require approval. Decisions which impact on a work team, a department, other projects or functions will require regular approval from the Team Leader. In addition decisions which impact on the customer or suppliers will require regular approval from the Team Leader.
There will be level of responsibility for others within the team due to the nature of the work. This will generally be for new recruits to the department and/or technical apprentices. Most of the time is spent performing work similar to that performed by the others in the team
Closing Date; 6th May at 4pm
Spirit AeroSystems is an equal opportunity employer and considers qualified applicants for employment without regard to race, colour, creed, religion, national origin, sex, sexual orientation, gender identity and expression, marital or civil partnership status, pregnancy, age, disability, veteran status or any other protected factor under federal, state or local law.