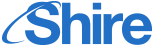
Job Information
Jensen Precast Vice President of Supply Chain in Reno, Nevada
Vice President of Supply Chain
Job Details
Job Location
Corporate - Reno, NV
Job Category
Executive
Description
What you’ll be Doing
The Vice President of Supply Chain is a vital member of our operations leadership team. In this role, you willtake ownership of supply chain strategies and processes for our precast concrete manufacturing business. This role will collaborate with operations, engineering, and sales teams to identify strategies aimed at improving reliability to customers while reducing product costs, enhancing profitability, and strengthening our competitive advantage. Key areas of responsibility will encompass inventory management/planning,enterprise resource planning (ERP) transactions/reporting, labor/capacity planning, and constraint-based scheduling. The supply chain function also supports the procurement of raw materials, standard costing, and fixed asset location management. The ideal candidate will have a demonstrated track record of strategic leadership, operational excellence, and supply chain optimization in a manufacturing environment.
Based at our corporate office in Reno, NV, and reporting to the COO, you’ll primarily work with the Company’s plant and corporate operations teams.
The principal accountabilities of this position include:
Provide strategic direction, leadership, and training to supply chain teams in our corporate office and plants. Foster a culture of collaboration, innovation, and continuous improvement. Mentor and develop team members to enhance their skills and capabilities.
Oversee the enterprise resource planning (ERP) tool as the business-side owner, focusing on enhancing its effectiveness and efficiency. Manage upgrades to the off-the-shelf ERP system. Develop and implement related procedures and training programs.
Lead efforts to optimize systems, business processes, information flow, metrics, and culture to achieve 99% accuracy in inventory records and 99% adherence to schedules. Maximizing reliability for our customers and evolving into an integrated business planning company through these initiatives is a strategic business objective.
Enhance supply chain processes already launched related to constraint-based scheduling, shop floor reporting, and product labeling/tracking.
Enhance our ability to track assets and utilization to support sales and operations planning and forecasting. Utilize variance data to identify inefficiencies and prioritize improvements.
Optimize inventory to reduce carrying costs and capital usage while maintaining sufficient supply to meet production needs and customer demand. Implement/enhance raw material warehouses. Ensure efficient sourcing of materials and components. Manage relationships and negotiate contracts with key vendors to optimize efficiency and reliability.
Assist in applying overhead costs to products using our activity-based costing practices. Streamline processes to decrease complexity and improve our ability to ensure accurate, up-to-date part input costs (e.g., per lb. for wire mesh, labor hours by tool vs. product). Utilize more granular measures of standard versus actual variances to appropriately allocate overhead costs and identify focus areas for margin/efficiency improvement.
Research, explore, and adopt readily available supply chain technology from other industries.
Qualifications
Who we are looking for
You’re enthusiastic and motivated in a fast-paced environment. You don’t take shortcuts. You’re safety conscious, not just for yourself but for the team.
The key attributes we’re looking for include:
Bachelor’s degree in supply chain management, logistics, engineering, business, or related or equivalent in relevant experience.
15+ years of manufacturing experience with a track record of success in optimizing operations and achieving results.
Industry experience in concrete manufacturing or building products sectors preferred.
Strong leadership skills, including maintaining a wide range of multi-site relationships at all levels of the organization, utilizing influence, communication, facilitation, and presentation to motivate teams and achieve excellence.
Professional communication skills and proven leadership capabilities
Excellent analytical and problem-solving skills with emphasis on data-driven decision-making.
Demonstrated ability to organize and execute assigned projects.
Proficiency in supply chain software and tools like ERP systems, inventory management software, and analytics platforms.
Experience in an integrated business planning environment or leading/launching an integrated business planning transformation preferred.
Familiarity with Oliver White Class A Standard for business excellence a plus
Certification in supply chain management is a plus (e.g., CSCMP, APICS)