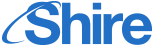
Job Information
Unither Pharmaceuticals Electrical Engineer in ROCHESTER, New York
Electrical Engineer
Who we are?
We are a French pharmaceutical industrial group, recognized for making affordable healthcare products that improve and simplify patients’ lives to as many people as possible.
With 30 years of technological expertise, we position ourselves as a world leader in sterile single dose with 10 sites on 4 continents and more than 2000 employees.
Since 2013, our site Unither Manufacturing LLC. based in Rochester (NY), specializes in the manufacture of Blow-Fill-Seal, Liquid Stick-Packs, Pharmaceutical bottles, Tablets and Capsules. It has more than 280 employees.
Your role
Reporting to the Senior Manager, Engineering, Validation, and Metrology,
The Process Controls Engineer is responsible for the planning, development, design and maintenance of control systems in the facility.
ESSENTIAL FUNCTIONS / RESPONSIBILITIES:
Technical Solutions (30%)
Support external engineering and design teams, as well as internal resources, to develop capital project proposals to address complex manufacturing issues.
Determines project specifications by studying product design, customer requirements, and performance standards; completing technical studies; preparing cost estimates.
Provides design documents for appropriate capital or improvement projects including P&ID drawings, process piping sizing, instrumentation, flow calculations, electrical/mechanical/pneumatic drawings, etc.
Support efforts within Engineering, Process Development, Operations, Quality and Validation departments through the use of Good Engineering Practices to develop requirements and recommendations for new manufacturing systems and modifications to existing systems.
Determines project schedule by studying project plan and specifications; calculating time requirements; sequencing project elements.
Capital Improvements Meet Requirements for Intended Use (40%)
Support management of complex, multidisciplinary projects including project spending and project scope changes to ensure that required deliverables are realized within approved spending limits.
Provide input to detailed project plans and timelines using project management tools such as Microsoft Project, and coordinates and ensures timelines with other departments (QA/Validation, Engineering, Operations, outside Contractors and Vendors, etc.)
Follow through on technical project responsibilities by identifying project phases and elements; assigning personnel to phases and elements; reviewing bids from contractors for technical accuracy.
Supports new equipment start up training initiatives as required. Works closely with maintenance and production to assure appropriate resources are trained on process and control systems.
Engineering Guidance & Advice (10%)
Provides Technical support for small molecule OTC and branded products.
Provides engineering support to corrective actions and deviations by identifying root cause and offering solutions.
With guidance, resolve high-level technical processing issues related to equipment operation.
Position is, at times, hands-on requiring trouble shooting of complex automated equipment and processes.
Acts as a subject matter expert for equipment operation and equipment efficiencies.
Assist with process improvement initiatives associated with delivering efficient process systems and controls.
Monitor and improve machine process, develop work instructions and train employees
Participate in implementing safety improvements
Design, program, analyze and repair electrical drives and control units
Provide technical expertise in troubleshooting Programmable Electronic Systems
Modify control system logic and industrial machinery to optimize equipment performance and control
Investigate operational problems affecting production in a systematic and methodical manner
KNOWLEDGE SKILLS & ABILITIES:
Strong background in technical troubleshooting, problem solving.
Detailed knowledge of equipment operation and validation requirements.
Proficient knowledge of pharmaceutical cGMP requirements and systems.
Knowledge of regulatory requirements for manufacturing of pharmaceutical products.
This position requires the ability to think in high level terms to develop technical solutions for new processes.It also requires the ability to think in specific, detailed terms when problem solving for existing processes.
Ability to foster and maintain an environment of proactive working practices, and effective communication within the group, and between the group and external functions.
Strong problem solving and investigation techniques.
Excellent written and oral communication skills.
Demonstrated performance in project management.
Strong organization skills with the ability to multi-task in a dynamic environment and balance multiple priorities.
Expertise with solid and liquid pharmaceutical manufacturing processes, equipment, and operations.
Must be capable of working independently, with self-initiative, self-motivation, and self-strategic direction, while also effectively working within team and matrix environment to influence and guide activity.
Proven ability to work on complex problems and interpret scientific data where analysis requires an evaluation of intangible variables.
Solid understanding and interpretation of Regulatory guidance documents and filing mechanisms.
Experience preparing and delivering technical presentations.
Ability to interact with people at all levels of the organization as well as some interaction with government agencies.
Your profile
EDUCATION & EXPERIENCE:
BS/MS degree in an engineering discipline, preferably in electrical or controls engineering.
5-7 years of controls engineering experience
Experience in high-volume, high-speed manufacturing
Experience in pharmaceutical, medical device industry strongly preferred
Hands on experience with packaging equipment, process and controls desired
PLC experience (Allen Bradley, B&R, Siemens)
Compensation range
85,000.00 - 100,000.00 USD
*The referenced compensation range represents the minimum and maximum compensation for this job. Individual annual salaries/hourly rates will be set within the job's compensation range, and will be determined by considering factors including, but not limited to, market data, education, experience, qualifications, expertise of the individual, and internal equity considerations.
Learn more about us:We are a dynamic company driven by a spirit of victory and are therefore pursuing strong growth while maintaining a close relationship with our customers and employees.
Our culture is based on 5 values: Respect, Responsibility, Trust, Courage and Innovation. We are committed to bringing these values to life with our employees by granting them a high degree of autonomy in the exercise of their profession and by encouraging their initiatives.
We are committed to providing them with working conditions and atmosphere that is conducive to their development and the expression of their potential.
We propose you to integrate a site that values the meaning of work and that entrusts our employees with a high level of responsibility.
Join us and make a difference!