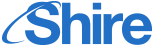
Job Information
Caterpillar, Inc. Quality Manager in Sagamihara, Japan
Career Area:
Manufacturing
Job Description:
Your Work Shapes the World at Caterpillar Inc.
When you join Caterpillar, you're joining a global team who cares not just about the work we do – but also about each other. We are the makers, problem solvers, and future world builders who are creating stronger, more sustainable communities. We don't just talk about progress and innovation here – we make it happen, with our customers, where we work and live. Together, we are building a better world, so we can all enjoy living in it.
Role Definition:
Oversees the administration and continual improvement of warehouse operations processes, with the focus on the quality management systems. Reporting to the position is the Logistics Engineer, the Packaging Analyst, the Quality Analyst and EWM Support Engineer.
Responsibilities:
• Work with Cat Teams to support the development of quality assurance strategies, processes, guidelines, and control plans which assure quality and reliability of our products. Leading the development and implementation of corrective action and preventive measures to achieve quality targets. Investigating and addressing trends on the internal and external non-conformance.
• Work with Service Providers to ensure the effective handling and inspection of Dealer Surplus Returns, Reman Core Returns, and Defective Parts. The verification and reworking of parts from engineering changes, identification of parts, and the reprocessing and repackaging of parts.
• Work with Service Providers on all warehouse audits involving inventory record, storage and shipping accuracies, the control and maintenance of storage concepts and necessary warehouse rearrangements are also being performed by the process Improvement team.
• Work with Service providers to ensure the effective maintenance and repair of the Cat own EWM equipment, infrastructure and security system to provide maximum availability and utilization of EWM’s system and assets. Escalates unresolved service requests within agreed timescales.
• Effective communication is maintained with Facility Planning, Distribution Planning and other Parts Facilities on new concepts, technology, systems and equipment and other improvements. Support and ensure the capital forecasts and expenditures are being initiated, coordinated and controlled.
• Any other duties as assigned by the manager in charge.
Degree Requirement:
Degree or equivalent experience desired
Summary of Skill Descriptors
• Knowledge of warehouse operation and quality management methods, tools, techniques, and ability to create and support an environment that meets the quality goals.
• Knowledge of the concepts, principles, and techniques of Lean; ability to use a structured approach to identify the causes of poor quality and the changes needed to prevent recurrences.
• Knowledge of collaborative techniques; ability to work with a variety of individuals and groups in a constructive and collaborative manner.
• The ability to speak, read and write in English and Japanese with minimal difficulty
Detailed Skill Descriptors
Planning: Tactical, Strategic: Knowledge of effective planning techniques and ability to contribute to operational (short term), tactical (1-2 years) and strategic (3-5 years) planning in support of the overall business plan.
Level Working Knowledge:
Contributes to short-term operational plans.
Anticipates and adapts to plan changes.
Monitors progress of work against plan as required to meet objectives.
Reports variances and makes agreed-upon corrections.
Under guidance, develops tactical plan for own direct responsibility.
Quality Management: Knowledge of quality management methods, tools, and techniques and ability to create and support an environment that meets the quality goals of the organization.
Level Extensive Experience:
Interprets results of quantitative and statistical tools and explains results to others.
Communicates key benefits of a quality management process.
Conducts and directs quality reviews.
Develops expertise in quality assurance tools, techniques, and standards.
Develops quality assurance processes based on Six Sigma, ISO 9000 or Baldrige principles.
Develops programs for motivating employees to meet or exceed quality goals.
Collaborating: Knowledge of collaborative techniques; ability to work with a variety of individuals and groups in a constructive and collaborative manner.
Level Working Knowledge:
Demonstrates experience participating in productive collaborative processes.
Under guidance, initiates collaborative meetings.
Assists in communicating shared goals with diverse groups and parties.
Helps promote collaboration across generations, functions, regions, and levels.
Helps solve business problems and meet business goals through collaborative processes.
Influencing: Knowledge of effective influencing tactics and strategies; ability to impact decisions within and outside own organization.
Level Working Knowledge:
Develops basic persuasive arguments.
Discusses organizational culture around providing input on decisions.
Uses active listening skills and probing techniques to surface opportunities to influence.
Identifies who the decision makers are and how they receive information.
Regularly presents ideas or suggestions to associates in persuasive terms.
Problem Solving: Knowledge of approaches, tools, techniques for recognizing, anticipating, and resolving organizational, operational or process problems; ability to apply knowledge of problem solving appropriately to diverse situations.
Level Working Knowledge:
Identifies and documents specific problems and resolution alternatives.
Examines a specific problem and understands the perspective of each involved stakeholder.
Develops alternative techniques for assessing accuracy and relevance of information.
Helps to analyze risks and benefits of alternative approaches and obtain decision on resolution.
Uses fact-finding techniques and diagnostic tools to identify problems.
Quality Risk Management: Knowledge of processes, tools, and techniques for Quality Risk Management; ability to implement the quality assurance process of assessment, control, communication, and review of risks to the quality of products.
Level Working Knowledge:
Documents the key steps of a unit-specific risk management process and associated procedures.
Explains and analyzes quality indicators and metrics relevant to own unit or function.
Highlights Quality Risk Management issues throughout the product life cycle.
Participates in a crisis management team to address quality issues.
Understands overall business objectives to effectively mitigate risks associated with quality.
Lean Manufacturing: Knowledge of the philosophy, principles and implementation approaches of lean manufacturing; ability to integrate and implement lean manufacturing philosophy into existing production and management processes.
Level Basic Understanding:
Cites examples of benefits and risks associated with implementing lean principles.
Describes basic tools for observing existing processes and identifying waste.
Cites industry or company examples of successful and unsuccessful lean implementations.
Identifies key lean principles and highlights of the lean manufacturing process.
Root Cause Analysis (RCA): Knowledge of the concepts, principles and techniques of root cause analysis (RCA); ability to use a structured approach to identify the causes of undesirable consequences in a manufacturing environment and the changes needed to prevent recurrences.
Level Basic Understanding:
Explains the rationale for finding and resolving the real cause of a problem rather than simply continuing to deal with the symptoms.
Describes the basic steps in an approach to root cause analysis (RCA).
Gives examples of problems that were resolved through root cause analysis.
Defines the terms 'Fixes that Fail structure' and 'Addiction structure'.
Posting Dates:
September 24, 2024 - October 7, 2024
Caterpillar is an Equal Opportunity Employer (EEO).
Not ready to apply? Join our Talent Community (http://flows.beamery.com/caterpillarinc/talcom) .