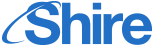
Job Information
Eaton Corporation Industry 4.0 & Special Process Lead in San Luis Potosi, Mexico
Eaton’s IS VEH VGNA division is currently seeking a Industry 4.0 & Special Process Lead.
What you’ll do:
PRIMARY FUNCTION
A. Improve plant performance, quality and cost by leading implementation of Industry 4.0 such as Real Time OEE, to provide real-time data collection and analysis, Digital Manufacturing through Process Simulations and CAD/CAM modeling providing Advanced Analytics, Strategic Automation by product family, Augmented Reality to provide Work and TPM instructions, SPC to improve quality performance and Additive Manufacturing for Operational excellence.
B. Ensure the proper functioning of special processes, robotics systems and continuous improvement projects. Analyzing advanced manufacturing performance to implement improvements, reducing safety risks, production cost, increasing efficiency and improving quality product for current and new processes and products.
ESSENTIAL FUNCTIONS
A. Develop and Follow up Long term Industry 4.0 implementation strategy.
B. Lead Internal Industry 4.0 Council.
C. Develop Business Cases for automation and RGV vehicles finding the best balance between cost and benefit using systematic approaches that integrate engineering, automation, ergonomic & environmental issues and information technology in the workplace.
D. Implement Automation and Transportation Robots (RGV) projects. Ensure Cost Out Metrics Related.
E. Develop analysis for OEE real time applicability and ensure the correct implementation of Thing Worx or any other application for data collection. Ensure Cost Out Metrics Related.
F. Promote and increase utilization of HoloLens to create Work Instructions, TPM, perform remote assistances and Layout visualization strategically in the plant. Ensure Cost Out Metrics Related.
G. Promote and increase utilization of Promodel or any other simulation software to create models and provide advance analytics for critical or strategic cells. Ensure Cost Out Metrics Related.
H. Promote and increase utilization of Additive manufacturing to improve safety, quality and efficiency by designing and producing tools, poke-yokes and gages internally with 3D Printing technology. Ensure Cost Out Metrics Related.
I. Promote and implement SPC for data collection and quality improvements.
J. Keep automation efficiently in the plant by Analyze problems and supervise corrections. Maintain and improve current manufacturing processes to produce parts to specification.
K. It supports the implementation of cost-saving projects, safety, quality, and improvements in production machinery.
L. Actively participate or champion in the continuous improvement process of the plant in key initiatives such as Value Stream Mapping, Continuous Flow Manufacturing, Setup Reduction, 5s, and Six Sigma.
M. Execute ELSS projects to eliminate waste for manufacturing processes.
N. Development improve and ensuring sustainability for the special processes in the plant.
O. Support PRO Launch - Participating in aspects related to manufacturing of new released components or assemblies. Review and evaluate new products, processes equipment and facility proposal. Lead and execute installation, runoff, and startup of transferred and new equipment. Complete runoffs and PPAP´s on time according to established schedules.
P. Motivate and coach employees to maintain high levels of satisfaction, productivity, and quality through effectively utilizing available rewards and recognition channels to encourage and promote desired behaviors and results
#LI-DS2
Qualifications:
SPECIALIZED KNOWLEDGE
A. Bachelor’s degree in mechanical, electrical, electronic or manufacturing engineering required.
B. 5 years experience in manufacturing, automation or engineering environment, ideally in the automotive industry.
C. English language at a conversational level required.
D. Knowledge of LEAN manufacturing techniques and manufacturing processes.
E. Demonstrated knowledge and training in assembly controls, automation, robotics systems, welding processes, Additive Manufacturing, error proofing techniques and problem solving.
F. Background or experience in quality basics such as statistical process control, capability studies and gage R&R´s.
G. Skills at interpreting mechanical drawings and basic use of CAD systems.
H. Knowledge of machinery functions (hydraulic, electrical, mechanical operations).
I. Black Belt (Six Sigma) would be a plus.
J. Project Management would be a plus.
K. CQI-12 Coating System.
L. CQI-15 Welding System
Skills:
ADDITIONAL INFORMATION
A. This position requires some travel.
B. It requires the use management skills, act as a liaison for associates at all levels.
C. Participate and assist to Industry 4.0 Meetings.
D. Develop and implement positive employee relations (Eaton Philosophy) to encourage employee involvement and to create an environment in which employees see no need for third party intervention.
E. Proactive & results driven.
F. Strong leadership and organizational skills, excellent written and oral communication skills and fluency.
G. Demonstrated and mature systems integration, planning and execution abilities are essential.
H. Demonstrated continuous improvement mindset.
I. Participate and assist in meeting all plant Environmental Health and Safety objectives.
J. Participate actively in Eaton’s initiatives such as community involvement, diversity and wellness.
K. Comply with the confidentiality agreements that are applicable and accept the data privacy policy accordingly
FUNCTIONAL COMPETENCIES
A. Business Systems and Practices
B. EBS Tool Integration
C. Manufacturing Process Design
D. Manufacturing Strategy Development and Execution
E. Manufacturing Value Stream Success Factors and Continuous Improvement
F. Program Management
G. Zero-Incident Workplace Culture
We are committed to ensuring equal employment opportunities for job applicants and employees. Our recruitment processes use balanced selection criteria and avoid unlawful discrimination against applicants on the basis of their age, colour, disability, marital status, national origin, gender, gender identity, genetic information, race or racial origin, religion, sexual orientation or any other status protected or required by law.