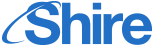
Job Information
Franklin Mountain Packaging Quality Coordinator in Santa Teresa, New Mexico
[[[VFS
[JOB SUMMARY
[[The successful candidate will ensure that quality standards are met and maintained by understanding, implementing, and enforcing compliance with customer, regulatory, and Franklin Mountain Packaging processes, policies, and procedures. The Quality Coordinator will assist with internal and external quality complaint resolutions, execution of audits, and ensuring efficient and smooth operations within the production facility.
[[[ESSENTIAL FUNCTIONS OF THE POSITION:
]{calibri=""}]{avenir="" next=""}]{avenir="" next=""}]{calibri=""}]{avenir="" next=""}]{calibri=""}]{calibri=""}]{avenir="" next=""}]{avenir="" next=""}
Ensure compliance with all standards, policies, and regulations for the safe, environmentally sound production for a quality product.
Drive plant accountabilities in tracking performance, resolution, and disposition of customer complaints, investigating critical quality defects on in-process and finished products, generation and analysis of quality data and reports.
Ensure all customer feedback is promptly dealt with and complaints are acted upon by the plant using root cause analysis and implementing corrective action.
Understand, implement, monitor, and enforce compliance with customer, regulatory and Franklin Mountain Packaging policies and processes.
Be able to track, analyze and lead initiatives for all internal quality and customer complaint issues.
Review, approve and execute facility and corporate standard operating procedures for site implementation.
Work closely with production managers to maximize product quality and reliability and minimize cost.
Coordinate and direct customer incident reviews.
Manage the CAPA (Corrective Action Preventive Action) system.
Gather and interpret performance data to create and execute facility improvement initiatives.
Provide daily quality data and feedback to facility and regional leadership.
Coordinate and execute investigation of detected risks or failures, complaints, and corrective/preventative actions.
Determine, document, and approve site-specific or one-time occurrences such as protocols (reworks, validations, etc.), deviations (planned or unplanned), waivers, or releases for materials and products as required.
Leverage enterprise technology to analyze quality complaints, track corrective and preventive actions, and use data to isolate and track defective parts per million, over shipments, and resolve issues related to rejected products when applicable.
Ensure team members are adhering to quality standards by actively engaging team members and supervisors on the production floor along with coaching, training, and conducting regular audits.
Be a change leader for BRCGS/ISO standards within the facility and be able to implement initiatives timely.
Lead a multidisciplinary team that identifies, evaluates, and controls hazards which are significant for product safety, quality and legality.
Demonstrate ability to execute projects in fast-paced environment and ensure that all quality reporting is completed timely and accurately.
[[Ensure a safety-oriented environment at the facility for all team members, vendors, and customers.< ]{calibri=""}]{avenir="" next=""}