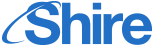
Job Information
Oberg Industries Validation Engineer in Sarver, Pennsylvania
Are you ready to take your validation engineering skills to the next level? Join our dynamic team of innovators at Oberg Industries, a leading contract manufacturer specializing in life-changing medical devices. We're seeking a Validation Engineer with a passion for quality, innovation, and the highest standards of excellence.
The Validation Engineer at Oberg Industries plays a crucial role in the development, execution, and documentation of validation activities related to the production processes, equipment, and systems used in the manufacturing of our medical devices. This role ensures compliance with regulatory requirements (e.g., FDA, ISO 13485, ISO 9001, and AS9100) and internal quality standards.
Key Duties and Responsibilities:
Lead validation protocols (IQ, OQ, PQ) for cutting-edge medical device manufacturing processes, equipment, and systems.
Conduct risk assessments and ensure that critical process parameters are identified, tested, and validated.
Collaborate with cross-functional teams to ensure product and process validations meet regulatory and customer requirements.
Write and review validation reports, ensuring that all required data is accurately captured and meets the required standards.
Support process improvements by performing validation gap assessments and implementing corrective actions as needed.
Ensure timely completion of validation activities in alignment with project timelines.
Maintain compliance with FDA regulations, ISO standards, and Good Manufacturing Practices (GMP).
Develop, execute, and maintain validation master plans.
Support internal and external audits by providing validation documentation and addressing auditor inquiries.
Other related duties as assigned.
Educational Qualifications and Specific Skills:
Experience working in the quality field, preferably as a Quality Engineer with either a medical device company or medical device contract manufacturer and/or a four-year college degree.
Experience working in ISO13485 / 21 CFR Part 820 or related quality system environment is required.
Experience with First Articles, Failure Modes and Effects Analysis (FMEA), Production Part Approval Process (PPAP) is preferred.
Experience with statistical analysis and SPC software programs is preferred (Minitab, QC Calc, etc.).
Experience with precision measurement equipment, such as drop gauges or surface analyzers, Coordinate Measuring Machines (CMMs), OGPs is preferred.
Internal auditing/supplier auditing experience preferred.
Working knowledge of FDA’s Process Validation requirements and methods, (IQ, OQ, PQ)
Working knowledge of APQP concepts and tools.
Working knowledge of computer programs such as MS Excel, Access, Word, PowerPoint, etc.
Must have good oral and written communication skills and have a keen attention to detail.
Must be able to travel domestically and internationally.
Must be a U.S. citizen or be able to comply with U.S. export regulations.
Must be able to wear personal protective equipment such as earplugs, safety glasses, and safety shoes.
Working Conditions: While performing the duties of this job, the employee is required to sit at a computer terminal and/or stand for extended periods of time. The employee may be required to observe and/or perform some manufacturing/inspection operations. This may involve occasionally working in and traveling through manufacturing areas. The employee must be able to wear personal protective equipment. While performing the duties of this job, the employee will regularly have to travel through other departments. The atmosphere is a combination of an office and manufacturing setting. This position requires on-site work. Remote work options are not available.
Benefits:
Competitive Pay
Medical, Dental and Vision Insurance (no premiums paid)
Medical benefit opt-out with Reimbursement option.
Health Savings Account (HAS)
Short & Long Term Disability (company paid, no contribution)
Death Benefit
401K Retirement Plan (with 4% employer match)
Employer Profit Sharing program
Quarterly Bonus Program (based on company performance)
Paid Time Off (earning up to 5 weeks)
9 Paid Holidays
Temperature-Controlled Work Environment
We also offer a family-friendly atmosphere and a number of perks for our employees such as Employee Referral Program Incentive Pay, Food Truck days, Health Club Membership Reimbursement, Tool Purchase program, Training and Development opportunities and much, much more!!
Oberg Industries is a local, family-owned, contract manufacturer and supply chain integrator providing tooling/metal stamping and precision machining services to many well-known companies around the world. Our passion is for precision manufacturing and our breadth of expertise enables us to provide cost-effective manufacturing solutions for the most demanding and complex production challenges for customers across the globe. Oberg Industries skilled employees stamp, grind, mill, turn, machine and design customized components and assemblies found in countless items that improve the quality of life for millions of people every day.
Our most competitive advantage is our skilled and innovative workforce. Oberg employees are among the best trained in the industry, supported by a culture of continuous learning that includes cross-training, apprenticeships, and advancement opportunities. Each employee plays a pivotal role in our ability to produce high quality parts. For more information about the company visit: www.oberg.com .
It is our commitment at Oberg Industries to create a diverse environment and we are proud to be an equal opportunity employer. EOE, including disability/vets.
Powered by JazzHR