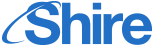
Job Information
Emmi Roth Production/Packaging Lead 2nd Shift in Seymour, Wisconsin
Production/Packaging Lead 2nd Shift
Location Seymour, WI
Apply Now (https://phh.tbe.taleo.net/phh01/ats/careers/v2/applyRequisition?org=ROTHKASE&cws=38&rid=1165)
It’s a GRATE time to start creating your BEST CHEESE MOMENTS by joining the EMMI ROTH Family!
From our plant floors to our corporate office, the Emmi Roth team is proud of the brands we make, the farmers we support, the people who enjoy our cheeses across the country and MOST IMPORTANTLY the EMPLOYEES who make it all possible. We are looking for energetic, hardworking people to help craft our specialty cheeses.
With three specialty cheese manufacturing facilities and our distribution center within the state of Wisconsin there is a HOME for YOU! A full TEAM IS A HAPPY TEAM who can spend more time with Family & Friends.
Join for the Job, Stay for the Career
EMMI ROTH provides on the job and paid training/certifications to assist in your development!
SUMMARY: The Production Lead is responsible for providing floor and department leadership for all facets of cheese production and can include intake, pasteurization, whey operation and sanitation (all depts.). They will act as a liaison for the team members as the first resource for reporting concerns or asking questions. Train, coach and develop production/sanitation employees as needed to ensure work is safe, efficient and product meets all quality specs. Will back up Supervisor as needed.
ESSENTIAL DUTIES:
Leads by example and acts as a liaison to internal and external customers, by reporting issues to supervisor, promoting the exchange of information and responding promptly and appropriately, while honoring commitments
Manage startup and/or end of day reporting. Communicate goals and KPIs, log and file paperwork as needed.
May manage work orders and supplies in JDE as needed throughout the day and EOD
Act as back up to the supervisor as needed
Lead the training of new employees in the department by assigning trainer, completing safety and NEO checklist, LOTO training.
Communicate with team members regularly to keep engaged and efficient, step in to cover breaks or time off as needed.
Understand all production processes and cross train as needed (i.e., whey, intake, sanitation)
Use basic hand tools to adjust machine operation and critical thinking to troubleshoot performance issues, partner with operators and maintenance team as needed.
Perform pre-operational inspections on equipment and chemicals recording data found and communicating issues in a timely manner
Preform monthly BBO’s as required to ensure team members are aligned with the safety processes and behaviors required
Record necessary documentation including pre-op inspections, cleaning forms, production charts and updating KPI boards.
Assist in the training of team members to build cross functional skill and growth within the cheese make related departments
Assist Supervisor with administrative tasks such as work SOPs, one-point Lessons and training development.
Communicate with Supervisor and/or Quality assurance regarding any production or sanitation issues
May use pallet jack to move supplies and product
Attend lead and department meetings
Actively participate to improve workplace safety, reduce waste, and improve factory efficiencies, lead by example
May be required to work overtime if deemed necessary
Complete all injury reports per the process and within time frames required. Work with Supervisor as needed
Complete all required training in a timely manner
Maintain a clean area without clutter, equipment, and personal sanitation
Adhere to ERU food safety policies and all government food safety and sanitation regulations (ex. FDA, HACCP, GMP, OSHA)
Preforms all other duties as assigned.
QUALIFICATIONS/MINIMUM REQUIREMENTS:
High School Diploma or GED
Previous lead experience - preferred
1 year of machine operating experience – preferred
Experience working within an ERP system – A plus
Communicate verbal and written effectively/legibly
Ability to add, subtract, multiply, and divide whole numbers
Basic computer skills including e-mail, word processing, spreadsheets, and scanner use
Ability to read and comprehend documents such as batch orders, control panel information and work order print outs
Ability to work with automated equipment
Ability to multi-task and prioritize under pressure
Ability to work in cross-functional teams
Work scheduled shifts and adhere to schedule as needed
Detail oriented and quality driven
Ability to work with minimum to moderate supervision beyond initial training
PHYSICAL REQUIREMENTS:
The physical requirements described here are representative of those that must be met by an employee to successfully perform the essential functions of this job. Reasonable accommodations may be made to enable individuals with disabilities to perform the essential functions.
While performing the duties of this job, the employee is constantly required to use hands and fingers to handle or feel objects and controls.
Constantly required to stand up to 8hrs during a shift
Constantly required to walk, bend, and reach with hands and arms
Constantly required to talk and hear
Constantly lift and/or move up to 10 pounds
Occasionally lift and/or move up to 30 pounds
Occasionally lift and/or move up to 50 pounds
Specific vision abilities required by this job include close vision, distance vision, color vision, peripheral vision, depth perception and the ability to adjust focus naturally or with correction.
(Occasionally = 1-25% of the time; Frequently = 26-75% of the time; Constantly = 76-100% of the time)
WORK ENVIRONMENT:
The work environment characteristics described here are representative of those an employee encounters while performing the essential functions of this job. Reasonable accommodations may be made to enable individuals with disabilities to perform the essential functions.
Constantly exposed to a high level of noise that may make it difficult to concentrate
Constantly exposed to wet, humid with slippery conditions, hot environment
Frequently exposed to food grade chemicals required for proper sanitation
Occasionally exposed to mold, dust, and cellulose (starch powder)
(Occasionally = 1-25% of the time; Frequently = 26-75% of the time; Constantly = 76-100% of the time)
The Best Cheese Moments are EMMI ROTH Moments!
Equal Opportunity Employer Minorities/Women/Veterans/Disabled
Back (https://phh.tbe.taleo.net/phh01/ats/careers/v2/searchResults?org=ROTHKASE&cws=38) Share