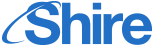
Job Information
Eaton Corporation Senior CI Engineer in Sincan Ankara, Turkey
On Senior CI Engineer role will be responsible for supporting deployment of the continuous improvement tools and processes of the Eaton Business System (EBS), including Continuous Improvement Framework (CIF), Eaton Lean Six Sigma (ELSS) and Operational Assessment (OpA) plants (Sincan-Temelli) in support of strategic goals and objectives.
What you’ll do:
Deputy CI Team Leader : Step in as deputy CI Team Leader when needed.
Lean Six Sigma Capability : Enhance organizational Lean Six Sigma tool usage and develop local CI Tool Champions through training and consulting.
Cultural Maturity : Lead the cultural maturity journey via Continuous Improvement Framework (CIF) deployment, including visual controls, process standardization, and Gemba walks.
Mentorship and Coaching : Mentor and coach site leadership and CI leaders on ELSS methodology, including CIF, HPWT, ELSS Tools, Rapid Improvement Events, and Lean Six Sigma Projects.
Assessments and Best Practices : Conduct annual Lean Six Sigma tool assessments, implement best practices, and ensure attainment of assessment and cost savings objectives.
Training and Problem-Solving : Act as an instructor and mentor for various training programs, lead problem-solving activities, and support Kaizen events and Six Sigma projects.
Qualifications:
BSC, MSC, Industrial Engineer, Manufacturing Engineer, Mechanical Engineer or related.
Minimum four (4) years of experience in a Manufacturing Environment.
Minimum three (3) years of experience in Lean, Continuous Improvement or Operational Excellence.
Skills:
Six sigma green/black belt.
Knowledge of lean manufacturing techniques – i.e. value stream mapping, one piece flow, etc.
Strong interpersonal and planning skills with proven ability to lead change through both direct and indirect (influencing) abilities.
Can effectively and comfortably speak to different levels of the organization; senior leaders to the factory floor.
Understanding of problem solving methodologies used in determining root cause and formulating corrective action(s) - i.e. thought maps, 8D, root cause analysis, Process Failure Mode Effect Analysis, Gage R & R, control charts, Pareto charts, etc.
Knowledge of industry and customer specific quality processes (i.e., ISO9001 etc).
Proficiency in MiniTab; knowledge of Computer Aided Design / Computer Aided Manufacturing.
Knowledge of Six Sigma concepts and tools as they relate to minimizing process / product variability – i.e. regression analysis, hypothesis testing, etc.
Knowledge of ELSS and EQS Tools.
What we offer:
Competitive compensation and benefits package.
Challenging projects in dynamic collaborative team.
We make your aspirations matter – Eaton encourages internal promotion, whenever possible.
We make your growth matter - We invest in our employees for the long term – not just with salary and benefits, but with ongoing learning and development opportunities made available through Eaton University.
We make your wellbeing matter – We put your health and safety first. Wellness at Eaton is more than a program, it’s about changing the environment by offering the right tools to help empower employees to make that happen.
We are committed to ensuring equal employment opportunities for job applicants and employees. Our recruitment processes use balanced selection criteria and avoid unlawful discrimination against applicants on the basis of their age, colour, disability, marital status, national origin, gender, gender identity, genetic information, race or racial origin, religion, sexual orientation or any other status protected or required by law.