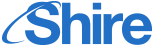
Job Information
Eaton Corporation Lead Manufacturing Engineer in South Molton, United Kingdom
Lead Manufacturing Engineer (South Molton, UK)
We are more than just a power management company, we are committed to inclusion, diversity, and sustainability. You will be part of a global team committed to delivering on our brand promise: "Make what matters work" We pride ourselves on building a culture that reflects our shared goals, beliefs, and attitudes.
We are ethical - We are passionate - We are responsible - We are efficient - We are transparent - We are learning. We are EATON!
What you’ll do:
• This position is responsible for supporting plant leadership in achieving business and financial goals by developing and maintaining robust manufacturing processes and leading continuous improvement / cost out initiatives across the organisation. Additional responsibility includes executing the organisation’s strategic plan consistent with UK & European legislation, and local regulations, established industry standards, and customer requirements
• With the team develop and maintain robust, cost efficient manufacturing processes and product structures consistent with lean manufacturing practices.
• Ensure root cause and failure analysis is performed as required.
• Lead cost-out events and promote culture of continuous improvement.
• Apply lean manufacturing techniques as means to eliminate waste and deliver products to customer’s expectations.
• Implement methods and practices to reduce variation.
• Develop team’s ability to understand source(s) of variation by applying Six Sigma Design and Development strategies.
• Participates in concurrent engineering efforts and critical design reviews to minimise product development costs and maximise useful life of products.
• Conducts Design For Manufacturing and Value Engineering initiatives as applicable.
• Develops work breakdown structures as a tool to develop cost estimates.
• Participate in new product development projects using ProLaunch as a tool to articulate deliverables and a vehicle to commit to schedules
• Coordinate manufacturing liaison/s for products from inception through shipment to customer.
• Develop and integrate new processes and methodologies as to provide competitive advantages for the business.
• Recommends Capital Appropriation Requests (including payback and net present value analysis) for acquisition of equipment to support emerging and existing technologies.
• Responsible for the training of associates as required, inline with APEX, OCA expectations etc.
• Communicates vision of organisation via verbal communication and actions.
• Coordinate with multiple functions to prepare consolidated plant, customer, and product status information and action plans.
• Develop, implement, and audit complex process procedures/work instructions (in-house and within the Supplier Base), when required, to alleviate production/quality problems and to achieve overall business objectives.
• Ensure robust plans are developed and monitored to ensure functional KPI’s are met
Qualifications:
• Relevant Engineering Degree, or equivalent qualification
Skills:
• Solid understanding of engineering design and product reliability concepts as to facilitate analysis of fluid dynamics, thermal dynamics, electronic circuits, etc
• Detailed knowledge of lean manufacturing techniques – i.e. value stream mapping, one piece flow, etc.
• Understanding of Six Sigma concepts and tools and where they relate to minimizing process / product variability – i.e. regression analysis, design of experiments, hypothesis testing, etc. Ensuring they are deployed appropriately
• Thorough understanding of problem solving methodologies used in determining root cause and formulating corrective action(s) - i.e. thought maps, 8D, root cause analysis, Process Failure Mode Effect Analysis, Gage R & R, control charts, Pareto charts, etc.
• Understanding of ProLaunch.
• Proficiency in various software applications – i.e. Computer Aided Design, Computer Aided Manufacturing, MS Office suite, MiniTab, etc.
• Knowledge of industry and customer specific quality processes (i.e., ISO9001, AS9100 etc).
• Knowledge of product and end user application/specifications, including product testing requirements. (design/process interface).
• Knowledge of manufacturing principles and technical specifications to support facilities competencies – i.e. metal cutting, tool design, injection moulding, welding, soldering, etc.
• Ability to lead cross-functional process improvement teams
• Understand application of SPC and gauge R&R.
• Managing a team, including coaching, mentoring & performance management
• Customer / Supplier interfacing (presentations, negotiations etc)
What We Offer To You
Competitive compensation and benefits package
Challenging projects in dynamic collaborative team
We make your aspirations matter – Eaton encourages internal promotion, whenever possible
We make your growth matter - We invest in our employees for the long term – not just with salary and benefits, but with ongoing learning and development opportunities made available through Eaton University
We make your contributions matter - reliability, safety, efficiency, and sustainability are at the core of our dedication to improving people’s lives and the environment through power management technologies.
We make your wellbeing matter – We put your health and safety first. Wellness at Eaton is more than a program, it’s about changing the environment by offering the right tools to help empower employees to make that happen.
#LI-JG1