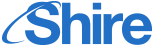
Job Information
Keurig Dr Pepper Sr Quality Assurance Specialist in Spartanburg, South Carolina
Job Overview
The Spartanburg operation is a state-of-the-art coffee roasting and pod packaging facility in addition to hosting a full beverage distribution center. Spartanburg is the largest KDRP manufacturing and distribution location. The site will operate on the foundational principles of TPM (Total Productive Maintenance); leverage the principles of Lean manufacturing. All associates at the Spartanburg site will have accountability to both a functional business unit in addition to the full site operation. The site will run on first-in-class enterprise IT and manufacturing execution systems with highly automated processing, packaging, and material movement equipment.
As a Senior Quality Assurance Specialist, you will be responsible for maximizing crew quality performance within the Spartanburg Site. In this role, you will be expected to have an in depth understanding of the input variables and measurement systems in our production equipment, and their impact on final product quality. This is a hands-on role that will require you troubleshoot quality issues with operations, monitor performance, drive continuous improvement, and continually strengthen a Zero-Defect quality culture across multiple lines. Working within a highly automated TPM-based environment, you will be expected to execute standardized processes following standard work, perform process audits, and facilitate structured problem solving to remove defects. Working in a High Performing Team-based environment, you will be looked upon to train, mentor, and guide the work of less experienced persons within your group, ensuring that they understand how to keep themselves and those around them safe as you collectively deliver world class cost, quality, and service performance. As a leader in business unit, you will be expected to regularly interact with site leadership to review quality performance results, communicate status of improvement initiatives and actively participate in plant-wide initiatives.
Shift & Schedule: This is a full time position on Days working our 2-2-3 schedule (see shift details). Flexibility to work overtime, weekends and holidays as scheduled is required.
Days: 6:30am-7:00pm
Week 1: Monday Tuesday Friday Saturday
Week 2: Sunday Wednesday Thursday
Compensation: This is a full-time salary position. Paid on a biweekly basis.
What you will do:
Safety: Deliver upon the site safety goal of zero injuries by being a role model in communicating, demonstrating and supporting safe behaviors, regularly completing behavioral safety observations and training others on the process, actively participate in safety meetings, own or co-own safety or environmental programs, regularly conduct safety audits and risk reduction initiatives and ensure 100% completion of all safety/regulatory training for you and your team
Quality: Drive a Zero-Defect quality culture. Improve the customer experience by understanding and training others on all quality control, Safe Quality Food, Good Manufacturing Practices, and other regulatory requirements.
Production: Assist in addressing equipment and material issues as they occur and partner across maintenance and operations to drive site performance. Lead and/or support cross-functional focused improvement initiatives to ensure quality risks are identified, prioritized and effectively addressed as part of improving efficiency and productivity
Write, interpret and provide training on Quality policies, standard operating procedures, and test methods.
Statistical Process Control expert for your business unit; define critical variables for evaluation, establish alarm conditions, and develop a control plan to respond to process deviations and drifts. Ensure operators are trained to use and interpret SAP application
Develop and conduct behavior-based audits to identify and remove gaps in our Quality System; collect, compile and report findings, and make recommendations for improvement
Analyze process and production data and ensure test and inspection plans are adequately matched to machine capability
Interact, collaborate and share best practices across crews and business units to ensure a standardized, best-in-class approach to quality across the organization
Work with the Quality Leader to ensure the Corrective and Preventive Action process is highly effective in the resolution of food quality nonconformances. Employ the use of effective root cause analysis tools, and lead/facilitate teams to find and execute sustainable solutions
Lead process improvement / problem solving efforts to include Kaizen events, Practical Problem Solving, 5-Why, data analysis and interpretation, and P articipate in the development of site Food Quality leading indicators so that Business Units may quickly identify gaps and implement improvements.
Develop a non-punitive approach to finding opportunities for improvement; drive a healthy, engaged quality culture at every level in the organization
P rovide technical leadership by participating in and leading Process Mapping, Process Capability Studies & FMEAs, training team members, facilitating improvement projects, incorporating quality into SOPs, and contributing to the continuous improvement of the TPM framework.
Exhibits a positive demeanor and models engaging communication styles and behaviors, demonstrates self-awareness and takes actions to continuously improve, does not engage in negative commentary, interacts respectfully and professionally with supervisors and coworkers
Own or participate in at least two elements of the quality or food safety management system such as Internal Audit, Document Control, Control of Nonconforming Material or HACCP Team
Total Rewards
Where Applicable:
Benefits eligible day one!!
Benefits, subject to election and eligibility: Medical, Dental, Vision, Disability, Paid Time Off (including paid parental leave, vacation, and sick time), 401k with company match, Tuition Reimbursement, and Mileage Reimbursement
Annual bonus based on performance and eligibilit
Requirements
Bachelor’s degree preferred
Five years of manufacturing experience, with at least two years in a leadership role or quality role
Mathematical skills to make production calculations and perform performance analysis
Six Sigma Green Belt or ASQ Certification Preferred
Able to facilitate and manage work projects involving cross functional teams to support quality metrics
Computer and software skills (Microsoft Office, SAP)
Excellent written and oral communication skills across all levels of the organization
Ability to stand/walk up to75% of the day in a shop-floor environment