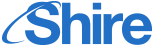
Job Information
Newmont data-careersite-propertyid="title" class="rtltextaligneligible">Condition Monitoring Technician in United States
data-careersite-propertyid="title" class="rtltextaligneligible">Condition Monitoring Technician
Date: Jul 2, 2024
Location:
Akyem, GH
Workplace Type: Onsite
Newmont is the world’s leading gold company and a producer of copper, silver, zinc and lead. The Company’s world-class portfolio of assets, prospects and talent is anchored in favorable mining jurisdictions in Africa, Australia, Latin America & Caribbean, North America, and Papua New Guinea. Newmont is the only gold producer listed in the S&P 500 Index and is widely recognized for its principled environmental, social and governance practices. The Company is an industry leader in value creation, supported by robust safety standards, superior execution and technical proficiency. Newmont was founded in 1921 and has been publicly traded since 1925.
At Newmont, people create the value in the metals we mine and are ambassadors in the communities where they live and work. As a team, we foster an environment in support of our people vision, where everyone belongs, thrives and is valued. We have built a diverse and inclusive workplace where our people can bring their differences to support delivering results together.
Our Africa operations employ approximately 5,900 employees and contractors, with the majority working at the Ahafo Mine. We offer an unparalleled blend of opportunity and career satisfaction with all the benefits you would expect from a global company. This, combined with our growth opportunities, makes Newmont a great company to work.
Our Akyem and Ahafo mines have made significant sustainable community development investments in our host communities. These include establishing Development Funds at our Akyem and Ahafo operational areas with each mine contributing US$1 per ounce of gold sold and 1% of net pre-tax annual profit into its community development fund.
Join us and unearth your potential in a global company that is at the forefront of shaping the future of the mining industry.
About This Role:
- To provide a reliable support service through the conduct of high quality condition monitoring of Process Plant equipment, via on-line and off-line data acquisition techniques and data analyses, testing and diagnoses, to prevent premature failures and maintain the optimal condition of the equipment at all times.
In This Role You Will:
Condition Monitoring
Conduct routine condition monitoring tasks on all rotating equipment and other tools, according to the established schedules and as per plant requirements.
Conduct extensive analyses on vibration and other data collected to diagnose / troubleshoot rotating machinery problems and recommend remedial measures.
Conduct thorough inspections on aspects such as temperature, pressure, vibration and monitor these elements on an ongoing basis.
Perform specialised non-destructive testing (NDT’s) toward the goal of maintaining equipment availability.
Conduct stress testing on various piping elements within the mine.
Conduct oil sampling activities on process plant equipment, as and when required.
Undertake maintenance work on parts / equipment, compile reports on field observations and factor results into weekly / fortnightly planning.
Produce daily reports indicating the jobs completed for the day and submit the report to the Mechanical Supervisor.
Undertake physical mechanical alignments of process plant equipment.
Complete preventative and corrective maintenance tasks, as assigned by the Mechanical Supervisor.
Report any major changes in equipment condition to the Mechanical Supervisor.
Participate actively in reliability improvement programs and Root Cause and Failure Analyses on all process plant equipment.
Collect data actively for analyses purposes.
Analyse and interpret data using CSI-RBM software.
Initiate corrective actions and propose improvements to enhance the reliability / availability of rotating equipment.
Participate in plant turnaround / shutdown activities, as and when requested by the Reliability Engineer.
Maintain various Condition Monitoring equipment files and associated data in the computerised system.
Propose measures to improve reliability and availability of plant rotating equipment, through the minimisation of failures.
Verify and provide detailed feedback on the condition of the equipment stating the sufficiency for plant production.
Provide overall support to the Reliability Engineer / Maintenance Management team.
Conduct and report on failure analyses and quantify potential value adds to mitigate this.
Follow-up on failure of notifications raised or deficiencies highlighted and work to close these gaps.
Assure that assets are able to perform as expected, to maximise the value generated.
Carry out statutory inspections on plant equipment including safety showers and eye washers, ladders, and pressure vessels.
Health, Safety and Environment
Comply with Newmont mine, health and safety regulations and Reliability Technician policies and procedures.
Accept personal responsibility for own health and safety.
Maintain and improve health and safety standards and practices.
Attend safety meetings.
Reporting
Maintain records of condition monitoring maintenance and repair work.
Compile reports on field observations and factor results into weekly / fortnightly planning.
Produce daily reports indicating the jobs completed for the day and submit the report to the Mechanical Supervisor.
Work Scheduling and Allocation
Accomplish work objectives by determining own work schedule, coordinate with support services and assign short-term tasks to other Technicians, as necessary.
Provide after-hours / standby maintenance back-end support.
Provide on-the-job training and guidance to Artisans, Service Persons and other equipment users.
Training & Experience
Formal Qualification (including Professional Registrations):
Diploma or equivalent technical qualifications in Engineering (Mechanical or Instrumentation preferred).
Specialised training in vibration analysis and other Condition Monitoring techniques.
Experience:
Minimum of 4 – 6 years’ experience in Condition Monitoring within the mining industry.
Working experience of PC-based On-Line and Off-Line Condition Monitoring Systems (Hardware and Software).
Additional Knowledge:
Strong knowledge of maintenance principles and industry standards.
Strong knowledge of the work management process.
Strong knowledge of planning and scheduling.
Knowledge of the condition / health of critical assets.
Knowledge of high-speed complex rotating equipment and associated maintenance fault analyses, diagnostics, techniques, repairs on pumps, motors, gearboxes, turbo compressors, screw compressors, extruders, reciprocating compressors.
Technical Skills:
Sound analytical and problem-solving skills.
Sound communication (written and verbal) and interpersonal skills.
Sound computer literacy skills (SAP, MS Word, Outlook and other Windows applications).
Ability to predict the onset of equipment failure that could lead to the loss of asset functionality.
Ability to troubleshoot, check tolerances on bearings and use precision measuring tool.
Ability to identify problems and to report by using technical names of equipment parts.
Behavioural Attributes:
Accuracy.
Detail focused.
Hand-eye coordination.
Independent.
Quality oriented.
Reliable.
Safety conscious.
Self-motivated.
Team player.
Technically inclined.
Working Conditions
The position is located at the Akyem mine site.
The physical demands and work environment characteristics described here are representatives of those that must be met by an employee to successfully perform essential functions of this job.
Personal Protective Equipment (PPE): Work requires mandatory PPE such as helmet, goggles, high visible clothing, safety harness, ear plugs and dust mask.
Incumbent may have to occasionally work overtime, when working on critical Process Plant equipment.
We understand no candidate will meet every single desired qualification. If your experience looks a little different from what we’ve identified and you think you can bring value to the role, we’d love to learn more about you!
Our business success comes from the accomplishments and well-being of our employees and contractors. Our goal is to build a workplace culture that fosters leaders and allows every person to thrive, contribute, and grow. We are committed to selecting and developing our employees, and to establishing a work environment where everyone can take an active part in reaching our strategic goals while feeling a sense of pride in working at Newmont.
Newmont seeks to recruit, hire, place and promote qualified applicants, meaning applicants who meet the minimum requirements of the position, without regard to personal characteristics such as gender, race, nationality, ethnic, social and indigenous origin, religion or belief, disability, age or sexual orientation or any other characteristic protected by applicable law. As part of our diversity efforts. females are encouraged to apply.
NOTE: Newmont does not ask for or require job applicants to pay money to apply or be considered for employment with the Company. In addition, Newmont does not ask potential job candidates to provide sensitive personal data without first submitting a job application through our secure, online portal, and only as requested for legitimate business purposes. If you are asked to provide money or sensitive personal data through any other means, do not respond and please report this immediately to it.sec@newmont.com .